I’ll tell you straight—most UK builders get plasterboard fixings wrong because they’re using the wrong screws. You’ve got coarse-thread for timber studs, fine-thread for metal, and each demands specific sizing to prevent stripping or poor grip. The bugle head design isn’t just aesthetic—it’s engineered to sit flush without tearing the paper face. But here’s what separates amateur work from professional installations: understanding the critical relationship between thread pitch, substrate material, and torque application that determines whether your fix will last decades or fail within months.
Key Takeaways
- Use coarse-thread screws for timber studs and fine-thread screws for metal studs to prevent installation failures.
- Ensure 25mm penetration into timber substrates and 10mm into metal substrates for secure plasterboard fixing.
- Choose screws with bugle heads to sit flush without damaging plasterboard surface during installation.
- Select screws compliant with BS EN 14566:2008 standards for building control acceptance in UK applications.
- Opt for phosphate-coated or zinc-plated screws to resist corrosion and ensure long-lasting wall fixes.
Types of Drywall Screws for UK Applications
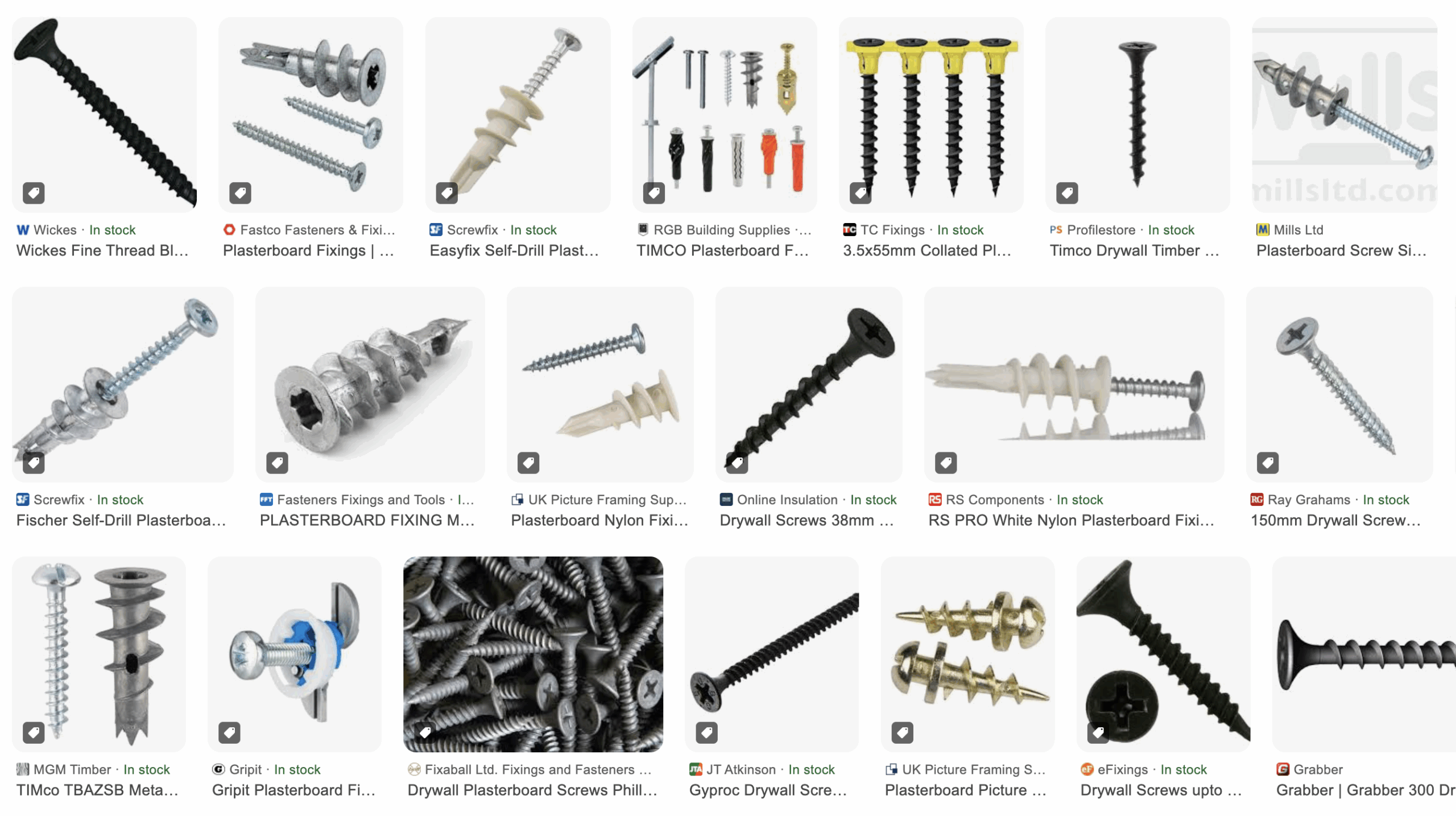
Selection of the appropriate drywall screw determines the success of your plasterboard installation. I’ll guide you through the essential types every UK tradesperson needs.
Coarse-thread screws are your go-to for timber stud work, providing superior grip in wooden frameworks. Fine-thread variants excel when fixing to metal studs, offering precise engagement without stripping. Self-drilling screws eliminate pre-drilling requirements for metal applications, saving valuable time on-site. An accurate assessment of your installation needs is crucial to avoiding costly repairs later on.
For efficiency-focused installations, collated screws integrate seamlessly with screw magazines like the SMD 57. Standard screws handle single-layer plasterboard applications—12.5mm or 15mm boards to 0.8mm gauge metal studs. When working with particularly thin metal sheets, A2 stainless steel self-drilling screws provide reliable chipless fastening for materials up to 2x 1.0mm thickness.
Each type serves specific substrate requirements. Match your screw selection to your framework material, and you’ll achieve professional results every time. The right choice prevents callbacks and guarantees structural integrity.
Thread Configuration and Material Compatibility
While thread configuration might seem like a minor detail, it fundamentally determines whether your plasterboard installation succeeds or fails. I’ve seen countless botched jobs where contractors grabbed the wrong screw type—coarse threads (W-type) belong in timber, fine threads (S-type) in metal substrates.
Here’s what separates professionals from amateurs: coarse threads deliver 9 threads per inch, maximizing wood grab and withdrawal resistance. Fine threads feature higher thread counts with 25° self-drilling points that pierce metal without pre-drilling. When you mismatch materials, you’re asking for trouble—coarse threads shred metal substrates, while fine threads won’t grip timber effectively.
Master this fundamental principle, and you’ll join the ranks of tradespeople who understand that proper thread selection isn’t optional—it’s the foundation of structural integrity. The bugle head design allows screws to sit flush below the plasterboard surface without causing paper damage or surface imperfections.
Sizing Guidelines for Timber and Metal Substrates
Getting your screw sizing wrong will compromise the entire installation—I’ve witnessed perfectly good plasterboard jobs fail because contractors didn’t grasp the fundamental penetration requirements.
For timber substrates, you need minimum 25mm penetration beyond the board thickness. That means 34.5mm screws for 9.5mm boards and 37.5mm for 12.5mm boards. Don’t cut corners with common 32mm screws on 9.5mm—you’re sacrificing holding power.
Metal substrates require only 10mm penetration, so 19.5mm screws work for 9.5mm boards and 22.5mm for 12.5mm boards. Always use fine-thread S-type screws for metal. These specialist screws feature deeper threads that provide superior grip compared to standard screws.
Remember: insufficient penetration creates weak points that’ll telegraph through your finish. Excessive penetration wastes material and risks damaging services behind the substrate.
UK Standards and Compliance Requirements
Since the Building Safety Act 2022 transformed UK construction regulations, I’ve seen contractors scramble to understand how these changes affect their plasterboard installations. You’ll need to comply with BS EN 14566:2008 for mechanical fasteners in gypsum plasterboard systems—this isn’t optional anymore. The Act demands stricter material selection, holding the entire supply chain accountable for safety compliance.
I’m witnessing BS 8539 becoming mandatory for post-installed anchors, while Eurocode 2 Part 4 raises fixing standards across the board. Your screws must meet toxicity and flammability requirements, with certified testing proving compliance. The Construction Fixings Association confirms these regulations are reshaping our industry. These specialized fasteners feature wide threads that create a firm hold without damaging the gypsum core, which is crucial for meeting current compliance standards. Don’t risk non-compliance—ensure your fixings carry proper certifications from recognized bodies, because building control won’t accept anything less.
Corrosion Resistance for Long-Lasting Performance
Beyond meeting compliance standards, your screw selection demands rigorous attention to corrosion resistance—I’ve watched too many installations fail because contractors overlooked this fundamental requirement. Phosphate coatings and zinc plating aren’t just protective layers; they’re your insurance against moisture-induced degradation that compromises structural integrity and fire performance.
I specify high-carbon steel grades like C1018 with phosphate bonding for superior adhesion, while zinc plating creates sacrificial anodes that absorb corrosive damage before reaching the substrate. These coatings withstand humidity fluctuations from -20°C to 80°C, resisting salt, alkali, and acidic agents without degradation.
Your installation deserves screws that preserve plasterboard fixings for 50+ years while reducing lifecycle costs by 30%. Professional-grade fasteners feature self-tapping points that eliminate pre-drilling while ensuring reliable penetration through metal sections up to 0.8mm gauge. Don’t compromise—corrosion-resistant fasteners eliminate premature failure and maintain building regulation compliance.
Installation Best Practices for Professional Results
While corrosion resistance protects your investment over decades, improper installation techniques can compromise even the highest-grade fasteners within months. I’ll walk you through the critical execution details that separate professional results from amateur failures.
Your screw pattern demands precision: 200-300mm vertical spacing with horizontal alignment at 300-400mm intervals along studs. I require minimum 36 screws per standard 2.4m × 1.2m board for proper load distribution. Drive each screw perpendicular to prevent cracking, ensuring heads sit flush without over-countersinking.
Fine-thread screws need 10mm penetration into metal studs; coarse-thread requires 25mm into timber. Pre-mark stud positions, use depth-adjustable drills for consistency, and apply PVA bonding to screw heads. The gypsum core provides excellent fire resistance properties, making proper fastening essential for maintaining the board’s inherent safety characteristics. Additionally, understanding renovation costs can help you budget effectively for your project. These fundamentals guarantee installations that’ll stand the test of time.
Conclusion
I’ve covered the critical specifications you’ll need for proper plasterboard installations. You’ll achieve superior substrate engagement by matching thread pitch to stud material—coarse for timber, fine for metal. Don’t compromise on bugle head geometry or corrosion protection; these factors directly impact your installation’s longevity. Follow BS standards religiously, and you’ll deliver professional-grade results consistently. Master these technical parameters, and you’ll never face premature fastener failure or substrate damage again.
References
- https://www.british-gypsum.com/products/fixing-products/british-gypsum-drywall-screws-25mm
- https://www.fastbuildsupplies.co.uk/fixings/screws/drywall-screws
- https://www.tcfixings.co.uk/articles/Coarse-Thread-vs-Fine-Thread-Plasterboard-Screws
- https://www.bolts.co.uk/which-drywall-screws-should-i-use
- https://www.ultimatehandyman.co.uk/forum1/viewtopic.php?t=54579
- https://www.hilti.co.uk/c/CLS_FASTENER_7135/CLS_SCREWS_2_7135
- https://www.bolts.co.uk/drywall-screws-c-4721/
- https://www.screwfix.com/guides/tools/screws-buying-guide
- https://www.senco.co.uk/en/products/fasteners/screws/screws-collated/p/39A35MCN
- https://www.siniat.com.au/en-au/resources-link-page/blog/2074117/