I’ve watched countless DIY enthusiasts struggle with subpar cuts simply because they grabbed the wrong blade. When you’re tackling your next UK project, whether it’s fitting skirting boards or building garden furniture, the TPI of your saw blade determines everything from cut quality to work speed. Most people don’t realize that using a 24-TPI blade for rough framing wastes time, while a 10-TPI blade will destroy your precision joinery work. Here’s what you need to know before making that first cut.
Key Takeaways
- TPI (Teeth Per Inch) determines cut quality: higher TPI creates smoother finishes, lower TPI cuts faster but rougher.
- Use 6-10 TPI for rapid rough construction work and 18-24 TPI for smooth finishing cuts on wood projects.
- TC/TCT tungsten carbide blades are ideal for hardwood, softwood, chipboard, and composite materials in DIY applications.
- Match blade size to your saw’s maximum diameter specification and ensure bore size compatibility for safe operation.
- Choose reciprocating blades with 8-11 TPI for demolition work and 14-36 TPI for precise metal cutting tasks.
Understanding TPI and Tooth Count for Circular Saw Blades
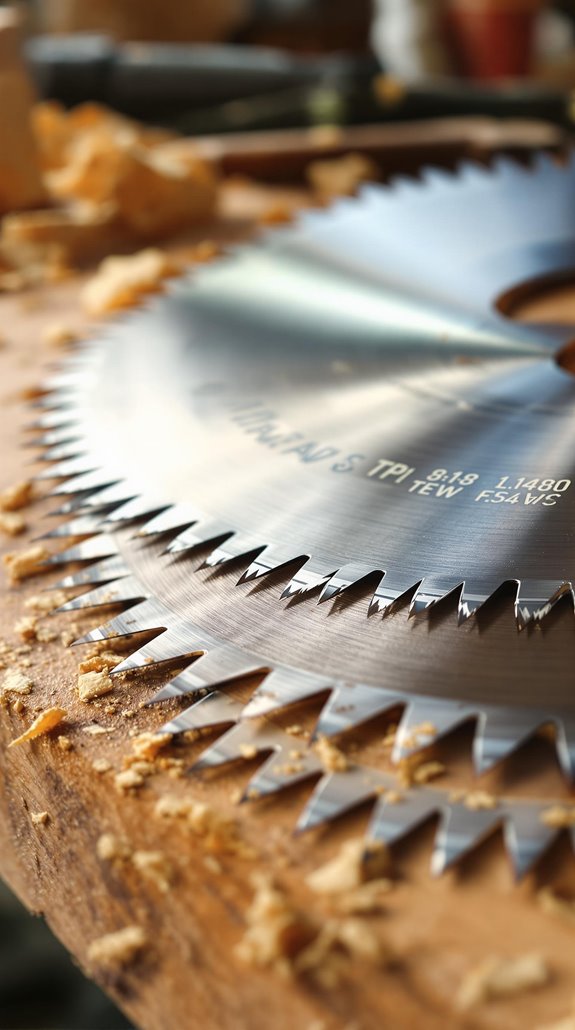
When I’m selecting a circular saw blade for my project, understanding TPI (Teeth Per Inch) becomes the foundation for making the right choice. TPI quantifies how many teeth exist within a one-inch segment of the blade’s cutting edge, and you’ll find this number clearly marked on the blade or packaging.
Here’s what separates us experienced DIYers from beginners: we recognize that higher TPI means more teeth packed together, delivering smoother cuts with less tear-out. Lower TPI means fewer teeth per inch, enabling faster but rougher cuts. I count teeth across a one-inch span to verify TPI when markings aren’t clear.
This measurement directly impacts your cutting performance – it’s the difference between professional-looking results and amateur work that screams “DIY disaster.” The tooth pitch between neighboring teeth also affects cutting efficiency and can reduce vibration during operation.
Material-Specific Blade Selection for UK DIY Projects
After determining the right TPI for your cut quality, I’ll guide you through selecting blades based on the specific materials you’re working with in your UK DIY projects.
For wood cutting, you’ll want TC/TCT (tungsten carbide tipped) blades for hardwood, softwood, chipboard, and composite materials. These blades offer superior durability and clean cuts across various wood types, making them ideal for enhancing aesthetic appeal in your projects.
When tackling non-wood materials, carbide (C) blades are your go-to choice for non-ferrous metals, plastic, and plexiglass. These specialized blades handle the unique challenges these materials present.
Chrome coated blades provide enhanced durability for intensive wood cutting applications, extending blade life considerably. Features like laser-cut expansion slots reduce vibration and noise during operation.
Naked blades (uncoated) are less durable and strong, making them suitable only for lighter wood cutting tasks where longevity isn’t critical.
Tooth Grind Types and Their Performance Characteristics
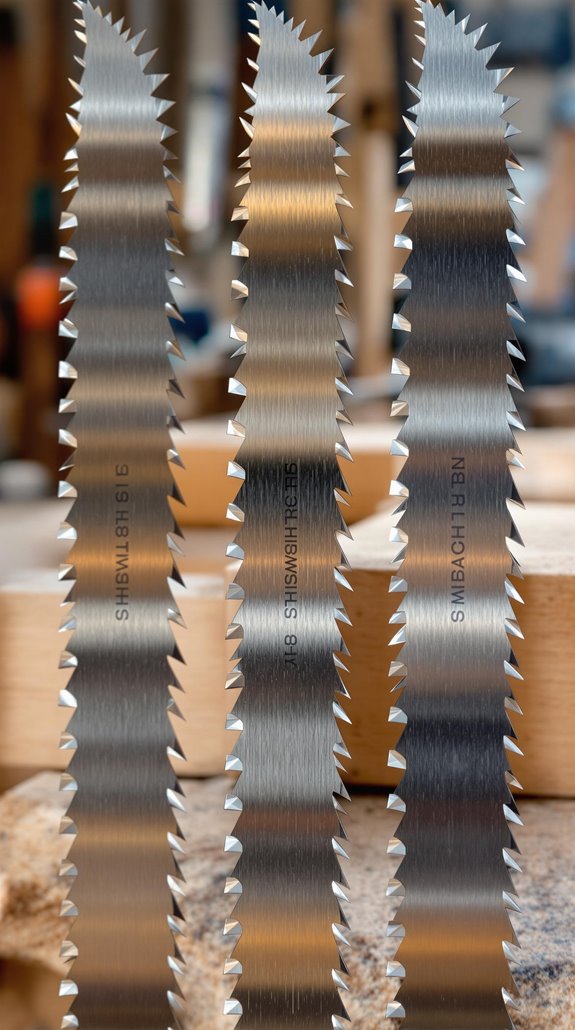
Beyond selecting the right material-specific blade, the tooth grind type determines how your blade performs during each cut. I’ll break down the four main grinds you’ll encounter in UK DIY stores.
Flat Top Grind (FTG) features square teeth that rip through solid wood fastest, though they leave rough surfaces. This type is often recommended for cost-effective renovations where speed is a priority. Alternate Top Bevel (ATB) uses angled teeth for clean crosscuts—perfect when finish quality matters. Combination (ATBR) blends both styles, making it ideal for general woodworking when you can’t switch blades constantly.
Triple Chip Grind (TCG) handles composites and metals brilliantly but struggles with solid wood. For most DIY projects, I recommend starting with ATBR blades—they’re versatile enough for mixed cuts while delivering decent results across different materials. Professional carbide blades feature thicker teeth of 2.5-3mm compared to cheaper alternatives, which significantly reduces chipping and enhances overall durability.
Blade Sizing and Compatibility With Your Saw
How do you guarantee your blade fits properly and performs safely? I always start by checking my saw’s maximum blade diameter in the manual – never exceed this limit. Common sizes include 200mm, 216mm, 250mm, and 300mm, with ranges from 85mm to 305mm for specialized work.
Next, I verify the bore size. You’ll encounter 5/8 inch, 1 inch, or 30mm (the modern standard). If there’s a mismatch, I use lathe-turned reducing rings with fibre washers and superglue to prevent dislodging.
I match blade diameter to my project needs: larger blades cut deeper but increase kickback risk, while smaller ones improve maneuverability for precision work. Consider the kerf width as well, since narrower blades may require a new riving knife to prevent binding during cuts. Additionally, using the right blade can help in early detection of subsidence, which is crucial for maintaining structural integrity. Remember, undersized blades compromise efficiency and finish quality, so choose wisely for ideal results.
Specialty Blades for Common DIY Tasks
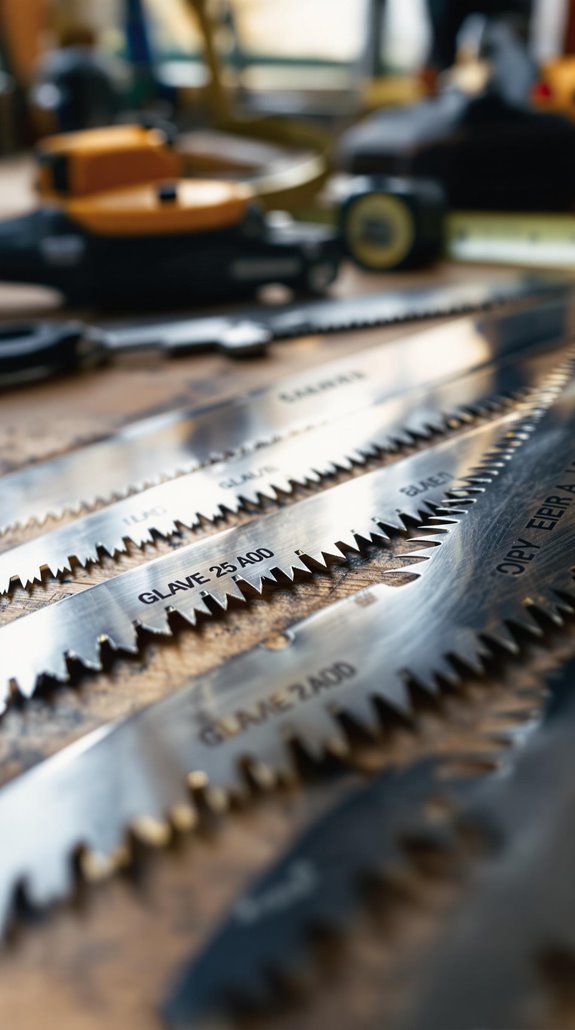
Once you’ve confirmed your blade fits properly, selecting the right specialty blade transforms your project’s outcome. I’ll guide you through the essentials for common DIY tasks.
For demolition work, I recommend reciprocating saw blades with 8-11 TPI. They’ll handle wood, plasterboard, nails, and screws efficiently without frequent changes. When speed matters over finish, choose 6 TPI blades for rapid wood cutting.
Metal cutting requires higher TPI than wood. Use 12-18 TPI for reciprocating saws, or 14-36 TPI for jigsaws and circular saws. These same reciprocating blades work brilliantly for finer wood finishes too.
For precision curved cuts, coping saws with fine teeth navigate tight radii perfectly. Panel saws with 18-24 TPI deliver smooth finishes, while 6-10 TPI handles rough construction work rapidly. Remember that TPI is counted from the bottom of teeth rather than the tips for accurate blade selection.
Choosing the Right Blade for Wood Projects
When selecting blades for wood projects, understanding tooth geometry makes the difference between professional results and frustrating tear-out. I recommend ATB blades as your go-to choice—they’ll handle both crosscuts and rips while delivering clean top surfaces that’ll make your projects look sharp.
For hardwood ripping, I’d grab a 24-30 tooth blade that cuts aggressively without bogging down. When you’re working with veneered panels or delicate stock, switch to 72-80 tooth blades to prevent chipping that’ll ruin your finish. It’s also crucial to manage timelines effectively to ensure that you have enough time to complete your project without compromising on quality.
Here’s what I’ve learned: match your tooth count to your priority. Need speed? Go lower. Want glass-smooth cuts? Choose higher counts, but feed slower to prevent burning. Evolution blades offer 3-year warranties that give you confidence in your blade investment for demanding projects. This approach consistently delivers results that separate serious DIYers from weekend warriors.
Metal and Composite Cutting Blade Requirements
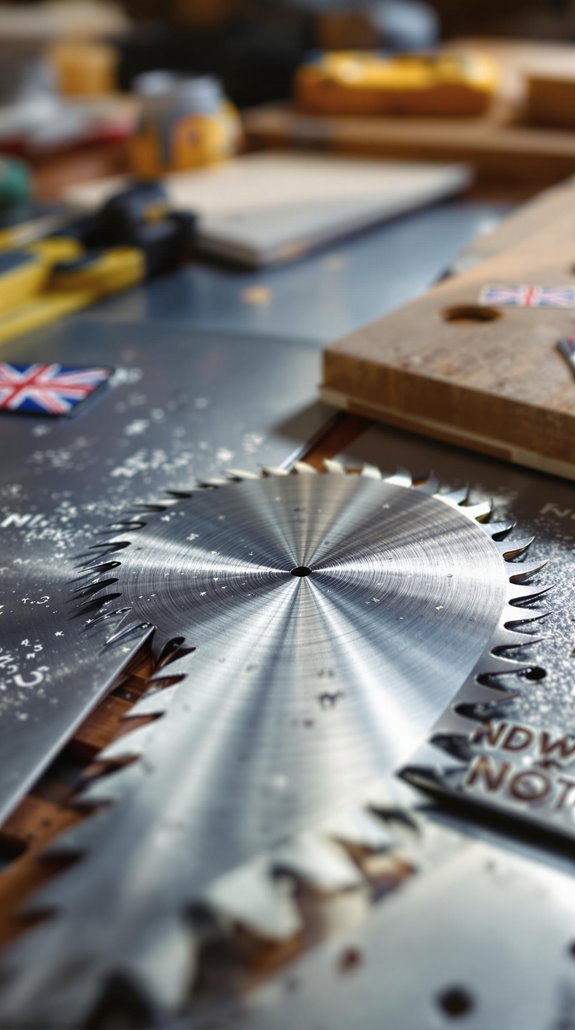
Metal and composite materials demand a completely different blade approach than wood cutting. I’ll guide you through the essentials that’ll transform your metal cutting results.
For metal work, you’ll need 14-36 TPI depending on your material thickness. I recommend 30-40 teeth for structural steel, balancing speed with finish quality. Thicker sections need lower TPI (14-24), whilst thin sheets require higher counts (30-40).
Look for cermet-tipped teeth or tungsten carbide tips—they’ll cut cold without work hardening your metal. High-speed steel with 5% cobalt handles tough steel alloys, whilst titanium nitride coatings reduce heat buildup considerably.
Choose blades with modified ATB geometry and expansion slots for heat dissipation. The proprietary tooth alignment process used in professional blades significantly reduces vibration and burring during cuts. You’ll achieve 100% more cuts per battery charge and reduce vibration by 30% with proper blade selection.
Safety and Maintenance Guidelines for Saw Blades
While proper blade selection determines cutting performance, implementing rigorous safety protocols and maintenance practices will protect you from serious injury and extend your blade’s operational life. I’ll establish a 300mm no-go zone beside blades and position guards 6mm above workpieces to minimise exposure. I terminate cuts 50mm before table edges to prevent body contact. Understanding how to secure profitable deals can be as critical as using the right tools in your DIY projects.
Regular visual inspections catch wear, rust, or misalignment before they become hazards. I verify blade sharpness and tooth integrity before each use, addressing defects immediately. Never attach toothed saw blades to angle grinders—the kickback risk is severe. I use manufacturer-recommended attachments only and employ mitre gauges for crosscutting rather than freehand techniques. Controlled feed rates prevent binding, whilst relief cuts reduce blade stress during curves.
When pointing stakes or cutting small workpieces, I always use a push-stick to maintain safe distance from the blade and prevent hand contact with sharp edges. Regular removal of off-cuts necessary to prevent jams and ejections.
Conclusion
I’ve covered the essential factors you need to take into account when selecting saw blades for your UK DIY projects. Remember, matching TPI to your material and desired finish quality is fundamental—higher TPI for precision work, lower for speed. Don’t overlook tooth grind types and blade compatibility with your saw. Whether you’re cutting wood, metal, or composites, the right blade selection will dramatically improve your results while ensuring safe operation. Choose wisely, and your projects will reflect professional-quality craftsmanship.
References
- https://www.getsawblades.co.uk/es/blogs/circular-saw-blades/understanding-the-blade-on-circular-saw-types-and-options-from-get-saw-blades
- https://www.thewoodhaven2.co.uk/threads/a-guide-to-circular-saw-blades.5266/
- https://www.homebuilding.co.uk/advice/types-of-saws
- https://shop4fasteners.co.uk/blog/types-of-saw/
- https://www.manomano.co.uk/advice/circular-saw-blade-buying-guide-3089
- https://benchmarkabrasives.com/blogs/cutting-tools/what-does-tpi-mean-for-saw-blades
- https://www.fengtai.com/blog/understanding-saw-blade-teeth-a-guide-to-tpi-atb-and-other-essentials.html
- https://www.empireabrasives.com/blog/what-does-tpi-mean-for-saw-blades/
- https://www.thesprucecrafts.com/how-many-tpi-should-my-saw-blades-have-3536401
- https://www.workprotool.com/news/how-the-teeth-per-inch-tpi-of-a-saw-blade-af-60464106.html