I’ve spent years helping homeowners navigate the complexities of RSJ installations, and I can tell you that choosing the wrong beam size or skipping proper structural assessments will cost you thousands in remedial work. Most people don’t realize that RSJ selection isn’t just about span calculations—it’s about understanding load distribution, building regulations compliance, and long-term structural integrity. Let me share the critical mistakes I’ve seen and the proven strategies that’ll guarantee your extension project succeeds.
Key Takeaways
- Calculate minimum beam depth as span divided by 15-20mm and use 46kg/m beams for loads exceeding 5 tonnes.
- Obtain structural engineer assessment and Building Regulations approval before installation to ensure Part A compliance and safety.
- Use temporary supports at 1.2m intervals with laser alignment tools and ensure 150mm minimum bearing length on padstones.
- Secure Party Wall Agreements for shared walls and verify ISO 9242 certification for hardened steel quality standards.
- Choose corrosion-resistant S355 steel grades and engage qualified contractors for professional installation to maximize structural integrity.
Choosing the Right RSJ Beam Size and Type for Your Extension Project
When selecting RSJ beams for your extension project, five critical factors determine the appropriate size and type: span length, supported load, beam profile, deflection limits, and material specifications. I’ll guide you through each consideration to guarantee you’re making informed decisions.
Your span length dictates minimum beam depth—calculate this as span divided by 15-20mm for ideal load distribution. For supported weight, heavier loads require thicker sections; you’ll need 46kg/m beams for loads exceeding 5 tonnes. Choose I-beam profiles for residential extensions over H-beams for better structural efficiency. Additionally, consider conducting a structural survey to identify any underlying issues that may affect your extension project’s foundation.
Verify your beams meet deflection limits per engineering standards and check ISO 9242 certification for hardened, tempered steel quality. All beams must comply with BS EN 10025 standards to ensure structural safety and regulatory compliance. These specifications assure your extension’s structural integrity and long-term performance.
Essential Installation Requirements and Professional Best Practices
Before you begin RSJ installation, you’ll need building regulations approval and must assess whether planning permission applies to your specific extension type. I’ll guide you through the essential requirements that’ll guarantee your project meets professional standards.
First, evaluate your property’s access challenges—they’ll directly impact labor costs and installation time. You’ll need to relocate utilities, with plumbers charging £30-£50/hour and electricians £25-£40/hour. Always confirm structural specifications with a qualified engineer for Part A compliance, as this will help you identify potential damp issues that could affect your extension.
During installation, I recommend using temporary supports at 1.2m intervals and laser alignment tools for precision placement. Confirm your padstones provide minimum 150mm bearing length and select corrosion-resistant steel grades like S355 for longevity. Steel RSJ beams are designed to withstand constant weight without deterioration over time. Finally, schedule building control inspections and monitor for structural issues post-installation.
Navigating UK Building Regulations and Structural Engineering Compliance
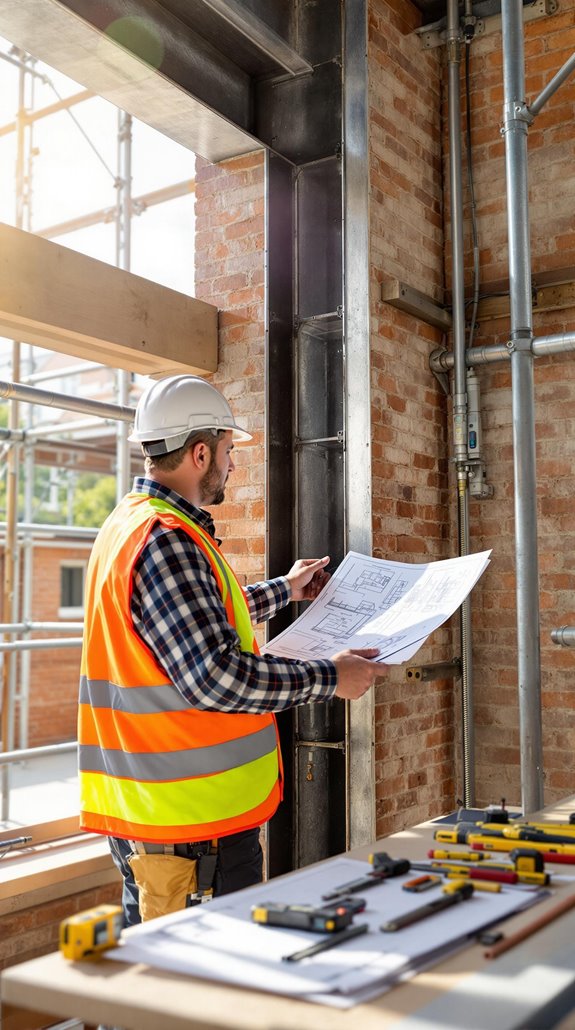
While your RSJ installation might seem straightforward, you’ll face a complex web of UK building regulations that demand precise structural engineering compliance. I’ll guide you through the essential steps that every successful home extension requires.
First, you’ll need a structural engineer’s certified assessment—typically £250—to calculate load capacity and beam specifications. Their plans are mandatory for building control submission, ensuring your project meets national safety standards and adheres to permitted development rights that may apply to your home.
You can’t skip building regulations approval for structural alterations. Your local authority will review the engineer’s calculations and conduct inspections during installation. Non-compliance risks enforcement actions and invalidates future property sales.
If your RSJ affects shared walls, secure party wall agreements before starting work. This prevents costly delays and legal disputes with neighbors who deserve proper notification. Remember that RSJs serve as the integral skeleton of your building’s structure, making professional installation absolutely critical for long-term safety.
Maximizing Structural Benefits for Open-Plan Living Spaces
RSJ beams transform cramped, compartmentalized homes into flowing, light-filled spaces that modern families crave. I’ll show you how to maximize these structural benefits for your open-plan renovation.
First, I recommend removing load-bearing walls between your kitchen, dining, and living areas. RSJs support the loads above while creating seamless connections that enhance social interaction. You’ll achieve exceptional strength-to-weight ratios, supporting heavy loads over long spans without intermediate columns cluttering your space. Furthermore, it’s essential to ensure that any modifications comply with planning permission requirements to avoid potential issues.
Next, consider installing larger window and door openings. RSJs enable expansive glazed areas that flood your interior with natural light. I’ve seen homeowners create stunning mezzanine floors using RSJs for vertical space optimization. The rolling steel manufacturing process ensures consistent quality and reliable performance across all beam applications.
The result? Visually expansive areas with flexible configurations that adapt to your evolving lifestyle needs while increasing property value by 5-15%.
Understanding RSJ Costs and Procurement Strategies Across the UK
When you’re planning an RSJ installation, understanding procurement strategies can save you 15-20% on total project costs. I’ll guide you through the key approaches that work best for UK home extensions.
Traditional procurement offers cost certainty through competitive bidding, letting you compare RSJ quotes precisely before construction begins. This process can help you avoid hidden costs that often arise during renovations.
For complex projects, prime contracting establishes long-term relationships with single-point responsibility, often delivering better value through established supply chains. New collaborative models encourage early contractor involvement, helping optimize RSJ design and sourcing. Modern procurement approaches emphasize early supplier engagement to improve project outcomes and reduce overall costs.
Choose your procurement route based on your risk appetite and project complexity—it directly impacts your RSJ costs and installation timeline.
Popular RSJ Applications in Residential and Commercial Extensions
Modern home extensions demand structural solutions that can handle significant loads while creating the open, flexible spaces today’s homeowners expect. I’ve seen RSJs transform countless projects by enabling complete wall removal for seamless kitchen-living areas and supporting wide-span openings that exceed traditional limits.
In residential work, I frequently specify RSJs for knock-through extensions and loft conversions where timber simply can’t handle the load. It’s crucial to have a well-defined budgeting plan before starting your renovation project to avoid unexpected costs. Commercial projects benefit from their ability to carry up to 12 tonnes across 12-meter spans without intermediate supports. You’ll find them essential for multi-level extensions, glass-enclosed spaces, and even heritage retrofits where compact profiles matter.
Their fire-resistant properties and pest-proof nature make them ideal for both residential open-plan designs and commercial retail spaces requiring flexible layouts. The precise dimensions of manufactured steel beams ensure consistent performance across all applications, whether custom cut for specific project requirements or used in standard configurations.
Conclusion
I’ve covered the critical aspects of RSJ implementation for your UK extension project. You’ll need proper structural calculations, certified materials, and building regulation compliance to guarantee success. Don’t skip the structural engineer consultation—it’s essential for safety and legal compliance. Remember to secure party wall agreements early, use temporary supports during installation, and follow deflection limits precisely. With careful planning and professional guidance, you’ll achieve a structurally sound extension that enhances your living space effectively.
References
- https://homebuildextensions.co.uk/rsj-steel-beam-installation/rsj-steel-beam-sizes/
- https://www.wall-away.co.uk/blog/correct-rsj-installation-for-self-build-extensions
- https://kevinfrancisdesign.com/blogs/design-ideas/why-steel-beams-are-essential-for-safe-home-extensions
- https://cahillsteelfabrication.co.uk/2023/01/27/should-you-use-rsj-beams-for-your-home-remodel/
- https://structuralengineercalcs.com/steel-beams-for-home-extension-a-structural-solution/
- https://hickmanandlove.co.uk/news/a-guide-to-rsj-beams/
- https://www.wadebuildingsupplies.co.uk/collections/rsj-beams
- https://www.metals4u.co.uk/materials/mild-steel/mild-steel-universal-beams-rsj
- https://www.myjobquote.co.uk/costs/installing-rsj
- https://www.steelbeaminstallers.co.uk/post/steel-vs-timber-beam-extension