I’ve been analyzing zinc cladding specifications for residential projects across the UK, and there’s a critical aspect that most homeowners aren’t considering when they’re drawn to zinc’s aesthetic appeal and durability claims. While the material’s 60-year lifespan and coastal performance sound impressive, the fire safety implications present complexities that could greatly impact your project approval and insurance coverage. The regulatory landscape has shifted dramatically since recent government testing protocols were implemented.
Key Takeaways
- Zinc cladding offers over 60 years lifespan with self-healing patina, reducing maintenance compared to timber or render alternatives.
- Non-combustible zinc achieves Class A flame-spread ratings, providing superior fire safety compliance in post-Grenfell building regulations.
- Aesthetic versatility supports both heritage renovations and contemporary designs while enhancing property value through modern upgrades.
- Excellent coastal performance withstanding 150 mph winds, with biannual freshwater cleaning maintaining appearance in marine environments.
- Zinc’s recyclability and energy efficiency align with sustainability goals while contributing to improved home energy performance.
Understanding Zinc Cladding Fire Risks in UK Residential Buildings
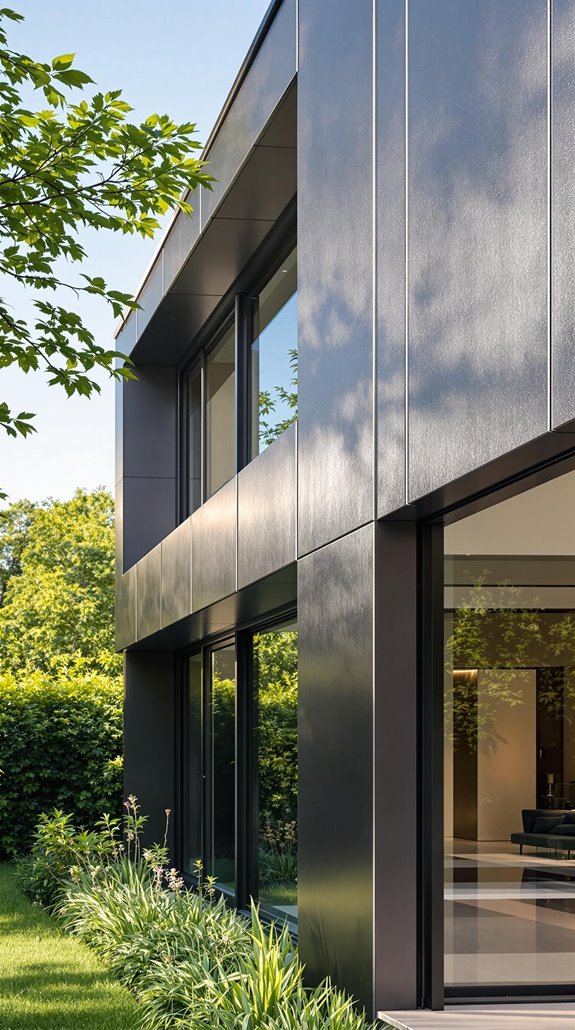
When selecting cladding materials for residential projects, understanding fire risks becomes vital in the post-Grenfell regulatory landscape. I’ve seen firsthand how combustible claddings like ACM with polyethylene cores create severe hazards, enabling rapid flame spread that can devastate entire buildings. The Grenfell tragedy demonstrated these risks catastrophically, leading to 72 deaths and exposing dangerous cladding on 1,700+ UK high-rises.
You’ll find zinc cladding offers inherent non-combustible properties with Class A flame-spread ratings, acting as a protective barrier against fire progression. Zinc cladding also meets various fire resistance standards that architects must verify for compliance in residential applications. Additionally, ensuring that all elements of the building adhere to flat roof gradient regulations is crucial in preventing water accumulation, which could exacerbate fire risks. However, I must emphasize that proper installation remains essential—gaps around windows or non-fire-rated insulation behind zinc can compromise safety. Today’s regulations mandate EWS1 certification for mortgage approvals, making compliant materials like zinc indispensable for maintaining your property’s insurability and market value.
Government Testing Results and Performance Comparisons
Following the Grenfell tragedy, the UK government commissioned extensive fire testing through the Building Research Establishment (BRE) in 2018 to evaluate non-ACM cladding materials that might pose similar risks. I’ll walk you through what these tests revealed about zinc cladding performance.
The BRE used 2m × 3m mock-up walls to simulate real fire conditions, testing zinc composite alongside copper, HPL, timber, and other materials. Zinc composite demonstrated the highest fire contribution among all non-ACM materials tested, burning through faster than alternatives. However, it didn’t replicate ACM’s catastrophic failure mechanisms.
While zinc showed concerning burn-through speeds and cavity fire propensity, the government concluded no tested materials matched polyethylene-cored ACM’s uniquely hazardous profile. The testing notably excluded polyethylene cored zinc panels, which may have performed similarly to the most dangerous ACM variants. This data informed current remediation priorities.
Why Zinc Cladding Appeals to Modern UK Homeowners
Despite zinc’s concerning fire performance in government testing, UK homeowners continue choosing this material for compelling practical reasons that extend far beyond initial cost considerations. I’ve observed that you’re drawn to zinc’s exceptional 60+ year lifespan, which withstands our harsh coastal conditions and unpredictable weather patterns. The material’s self-healing patina eliminates tedious maintenance cycles you’d face with timber or render alternatives. Furthermore, thorough planning is essential to ensure that the installation aligns with your renovation goals.
What truly sets zinc apart is its aesthetic versatility. You can achieve both heritage-appropriate renovations and cutting-edge contemporary designs using the same material. The malleability allows complex architectural forms that rigid materials simply can’t match. Modern homeowners often choose cassette panels for their quick installation and integrated insulation benefits. Additionally, zinc’s 100% recyclability and lower energy production requirements align with your sustainability goals while qualifying for BREEAM certifications. These practical advantages explain why you’re prioritizing long-term performance over initial fire testing concerns.
Fire Safety Standards and Certification Requirements
Since the Grenfell Tower tragedy reshaped UK building regulations, you’ll need to navigate increasingly stringent fire safety standards when specifying zinc cladding for your project. I’ll guide you through the essential requirements that’ll keep your installation compliant and safe.
Your zinc cladding must achieve Class A flame-spread ratings and A1/A2 Euroclass classifications. For buildings exceeding 18 meters, you’ll face mandatory fire risk assessments and BS 8414 testing requirements. Below 11 meters, you’ve got more flexibility, though competent person assessments remain essential.
You’ll need manufacturer certifications specific to your location, plus third-party validation through LABC or BBA approval. The documentation must verify flame spread, smoke production, and structural integrity. Since zinc naturally meets non-combustibility thresholds, you’re already ahead of projects using combustible alternatives. Additionally, it’s crucial to adhere to updated building codes to ensure compliance with national safety standards.
Regular inspections of your cladding system will help identify potential issues before they become serious safety concerns. These detailed checks ensure ongoing compliance and can prevent costly remediation work down the line.
Real-World Performance: Coastal Residential Applications
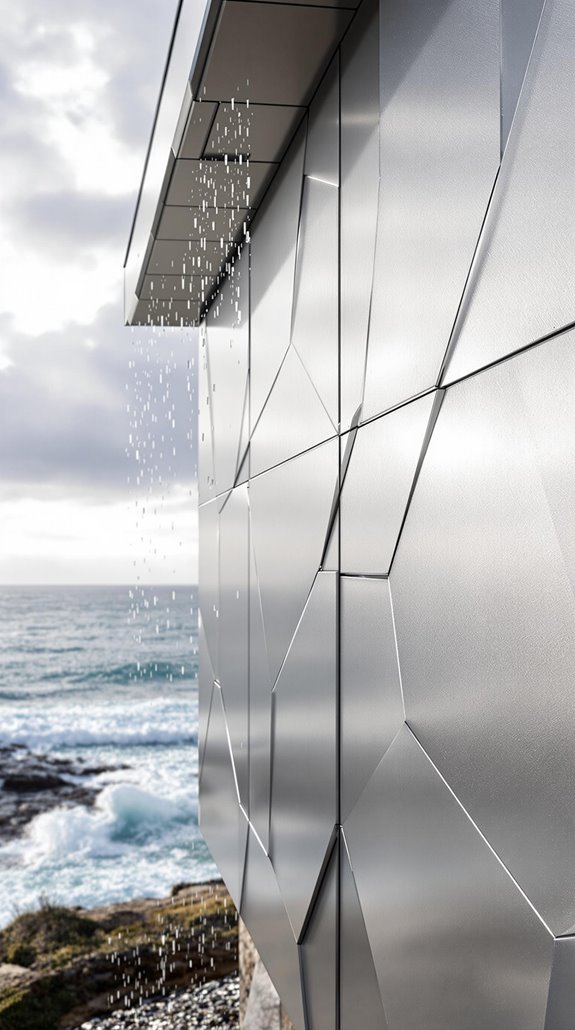
When you’re specifying zinc cladding for coastal residential projects, you’ll find that real-world performance exceeds laboratory predictions in marine environments. I’ve documented installations withstanding 150 mph winds and salt-driven corrosion for over 70 years, validating zinc’s exceptional coastal resilience.
You’ll notice VMzinc Pigmento and Strat ranges deliver superior results through pre-weathered surfaces and protective lacquers. The lighter finishes, particularly blue-gray, minimize visible salt deposits that concern many coastal homeowners. I recommend avoiding zinc for soffits and gutters where salt accumulates on unrinsed surfaces—timber alternatives perform better there.
Your maintenance schedule should include biannual fresh water cleaning to remove salt residues. The patina development accelerates in coastal zones, naturally lightening without structural compromise while maintaining the protective barrier that outperforms coated steel and aluminum. The zinc material ensures safe water runoff due to its low toxicity properties, making it environmentally responsible for coastal residential applications.
UK Cladding Statistics and Regulatory Landscape
The scale of UK cladding defects reveals a massive infrastructure challenge that directly impacts your project planning and material selection decisions. With 5,052 residential buildings identified as having unsafe cladding, you’re operating within a heightened regulatory environment that demands careful material choices. I’ve observed that only 33% of affected buildings have completed remediation, despite £2.7 billion in allocated funding. This creates opportunities for us zinc cladding professionals, as property owners seek compliant alternatives. The Cladding Safety Scheme monitors buildings ≥11m height, establishing clear performance standards you’ll need to meet. In addition, understanding the nuances of Permitted Development Rights will help homeowners maximize their renovation potential while ensuring compliance with local regulations.
Monthly DLUHC data releases track remediation progress across multiple programmes, giving you real-time insights into market demand. The ongoing monitoring of building safety ensures that remediation efforts remain a critical priority for authorities. Understanding these regulatory frameworks helps you position zinc cladding as a safe, compliant solution for clients traversing this complex landscape.
Conclusion
I’ve outlined zinc cladding‘s technical advantages for your UK residential project. You’ll get 60+ years of performance with minimal maintenance requirements due to its self-healing patina properties. The material exceeds fire safety standards while delivering superior coastal corrosion resistance. I’d recommend zinc cladding if you’re prioritizing long-term durability, energy efficiency improvements, and architectural flexibility. You’ll need to verify local building regulations and certification requirements before proceeding with your installation project specifications.
References
- https://assets.publishing.service.gov.uk/media/628355dc8fa8f5561a6b2686/11-18m_buildings_publication.pdf
- https://acelabusa.com/product-guides/zinc-cladding
- https://www.insidehousing.co.uk/news/non-acm-products-do-not-pose-same-threat-as-grenfell-style-cladding-government-claims-as-tests-released-65940
- https://www.propertychecklists.co.uk/articles/need-know-more-about-cladding-here-are-the-essentials
- https://www.ribaj.com/products/vm-zinc-housing-sector-specifications-uk
- https://www.preventionweb.net/understanding-disaster-risk/terminology/hips/tl0006
- https://www.riskstop.co.uk/risk-guides/cladding-fire-risk-assessments
- https://en.wikipedia.org/wiki/United_Kingdom_cladding_crisis
- https://www.gov.scot/publications/scottish-advice-note-determining-fire-risk-posed-external-wall-systems-existing-multi-storey-residential-buildings/pages/5/
- https://www.thefpa.co.uk/news/news/news_detail.non-acm-cladding-does-not-pose-same-threat.html