I’ve witnessed countless UK plumbers face devastating consequences from push-fit connector failures that could’ve been prevented with proper knowledge. While these connectors offer undeniable convenience, they’re riddled with hidden pitfalls that can result in catastrophic water damage, insurance nightmares, and costly repairs. From material compatibility issues to long-term seal degradation, there’s a minefield of technical challenges that even experienced professionals sometimes overlook. Let me expose the critical disadvantages you absolutely must understand before your next installation.
Key Takeaways
- Push-fit connectors can fail catastrophically if pipes aren’t fully inserted or systems lack proper pressure testing before commissioning.
- Mixing different brands or using non-WRAS approved components creates compatibility issues that increase leak risks and system failures.
- Rubber seals degrade over time from environmental exposure and water hammer, leading to sudden failures and potential flooding.
- Installation requires specialized tools like pipe cutters, deburring tools, and calipers plus proper technique to avoid costly mistakes.
- Many UK insurers exclude push-fit systems or impose higher excess fees, potentially voiding coverage for water damage claims.
Installation Errors That Lead to Catastrophic Water Damage
When push-fit connectors fail catastrophically, the resulting water damage often stems from preventable installation errors that compromise the system’s integrity from day one.
I’ve witnessed countless failures where pipes weren’t fully inserted into fittings, ignoring that critical “click” confirmation we all know signals proper engagement. Short-stabbing is particularly devastating—when pipes aren’t pushed to required depth, they’ll disconnect under pressure, flooding your property.
Angular stress from improperly supported pipe runs creates relentless strain on joints, while thermal expansion forces tear connections apart. Skipping pre-commissioning pressure tests to meet deadlines compounds these risks exponentially.
The most costly mistakes involve concealed installations without access panels, where leaks remain undetected until catastrophic damage occurs behind expensive finishes. Sudden pressure variations can displace internal components, breaking seals and causing immediate flooding in hidden areas.
Material Compatibility Issues and Usage Restrictions
While push-fit connectors offer impressive versatility across multiple pipe materials, their compatibility isn’t universal—and mixing incompatible components creates serious failure risks that I’ve seen devastate entire installations.
Brand-specific inserts must match your fitting manufacturer exactly. I’ve witnessed catastrophic leaks from contractors mixing JG Speedfit inserts with generic fittings, thinking they’d save money. Don’t make this mistake—incompatible components guarantee joint failure.
Non-WRAS approved fittings lack proper corrosion resistance and pressure tolerance. You’ll face premature failures in demanding applications like hydronic heating systems. Quality push-fit fittings from reputable manufacturers undergo rigorous testing by British Standards Institute and WRAS to ensure they meet high performance standards.
Usage restrictions are equally critical. Never install push-fits in inaccessible locations like enclosed walls—seal degradation risks aren’t worth potential water damage. High-rodent environments also pose seal integrity threats that traditional soldered joints better withstand.
Aesthetic Compromises in Visible Plumbing Areas
Although push-fit connectors excel functionally, their aesthetic impact becomes problematic when plumbing runs remain visible in modern architectural spaces. I’ve observed how their bulky profile creates obtrusive appearances in open-plan kitchens and bathrooms, where slender copper fittings would maintain visual harmony. You’ll find these plastic fittings compromise minimalist interior aesthetics with their protruding bulk and matte surfaces that show scratches more visibly than metal alternatives.
The material finish limitations become particularly apparent in designer interiors where pipes serve as architectural features. I’ve noticed how plastic fittings can’t replicate the metallic sheen required for contemporary accent themes or heritage coppersmithing in period properties. When mixing materials, visible shifts create disjointed appearances that break visual flow in luxury installations, ultimately affecting property valuations in high-specification renovations. The higher upfront costs of push-fit systems add financial burden to aesthetic compromises, making traditional methods more appealing for visible installations despite labor considerations.
Long-Term Reliability Concerns With Rubber Seals
Beyond aesthetic concerns, push-fit connectors carry significant long-term reliability risks centered on their rubber seal dependency. I’ve observed that environmental exposure accelerates rubber hardening through heat, UV, and chlorine contact, leading to cracking within 5-10 years. Mechanical stress from water hammer compounds this degradation, while chemical reactions with water additives reduce seal elasticity far below advertised warranty periods.
What’s particularly concerning is oxygen diffusion through plastic pipes, which degrades rubber faster than metal systems. Unlike gradual soldered-joint leaks, rubber seal failures often occur suddenly without warning signs. I’ve documented cases where seal compromise leads to complete fitting separation under mains pressure, causing catastrophic flooding. However, many of these failures stem from incorrect installation rather than inherent fitting defects, as proper fitting procedures are crucial for long-term system reliability. This unpredictable failure mode makes push-fit connectors unsuitable for critical applications where reliability matters most.
Essential Tools and Skills Required for Proper Installation
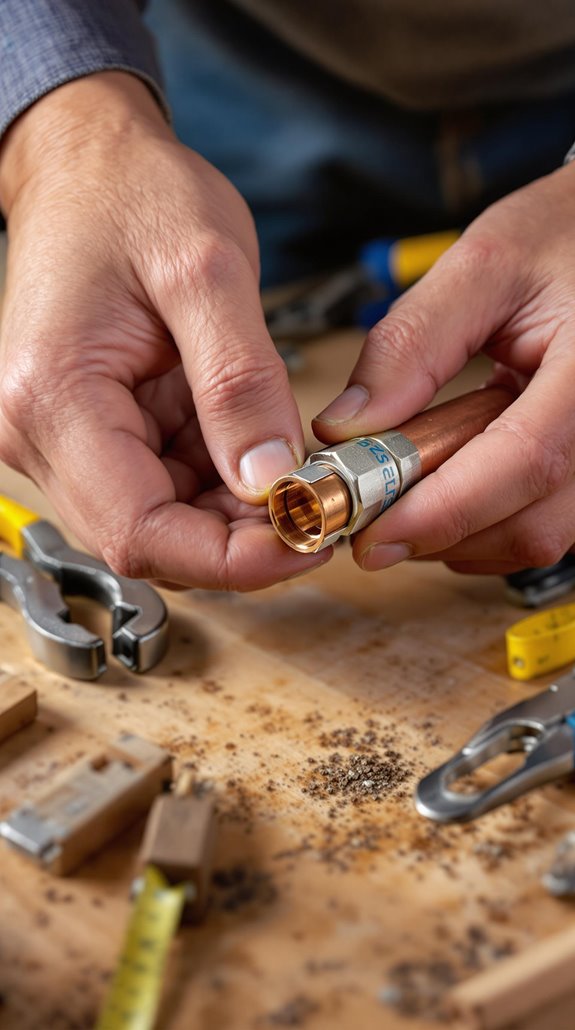
Despite marketing claims of “simple installation,” push-fit connectors demand specialized tools and precise techniques that many installers overlook. I’ve witnessed countless failures from installers who assume these fittings are foolproof. You’ll need pipe cutters for square cuts, deburring tools to prevent O-ring damage, and chamfering tools to avoid seal displacement. Calipers aren’t optional—they’re essential for verifying diameter compliance.
Proper technique requires recognizing that audible “click” confirmation and testing insertion depth against fitting indicators. I always pull-test each joint before pressurization and verify pipe inserts are correctly positioned. The rotation alignment feature becomes worthless if you don’t achieve proper initial insertion.
Without these tools and skills, you’re setting yourself up for callbacks and reputation damage that seasoned professionals work hard to avoid.
Higher Costs Beyond Initial Material Savings
While push-fit connectors appear cost-effective upfront, the hidden expenses accumulate quickly through specialized installation requirements and long-term maintenance needs.
I’ve discovered that plastic push-fit joints demand additional clips to prevent loosening or catastrophic failure, immediately increasing your material costs. Without proper clipping, you’ll face expensive water damage repairs that dwarf any initial savings. The vulnerability to rodent damage creates another costly concern – mice and rats can chew through plastic pipes, requiring emergency repairs that copper systems never experience.
Installation complexity drives up labor costs too. Ensuring correct push-fit installation requires skilled technicians who understand the nuances of these systems. The emphasis on proper technique means you can’t cut corners with inexperienced installers, making professional installation more expensive than anticipated. The installation errors common with push-fit systems increase the risk of callbacks and additional repair costs that traditional soldering methods rarely encounter.
Professional Training Requirements for Safe Installation
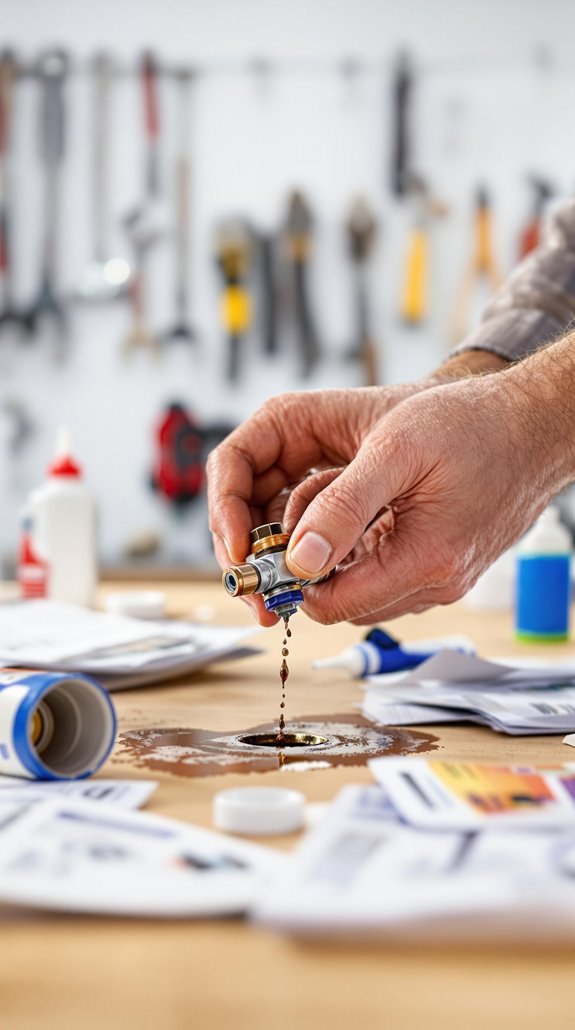
Installing push-fit connectors safely requires specialized training that goes far beyond basic plumbing knowledge. I’ve witnessed countless installations fail because installers skip critical preparation steps like proper deburring and SmartSleeve™ installation. You can’t simply push pipes together and expect reliable connections.
Master the insertion verification techniques – In4Sure™ technology and visual depth indicators aren’t gimmicks, they’re essential safety protocols. I’ve seen professionals struggle with twist-lock mechanisms that must audibly click for secure copper connections. The tug tests and 24-hour pressure maintenance aren’t optional steps you can shortcut.
Your reputation depends on understanding staged pressurization sequences and BS EN 806-2 standards. Without proper training on these manufacturer-specific protocols, you’re risking system failures that could cost thousands in repairs and damage your professional credibility.
Temperature and Environmental Limitations
Even with proper installation training, push-fit connectors face significant operational boundaries that can compromise system integrity. I’ve observed that plastic fittings can withstand temperatures up to 114°C intermittently, but they’ll degrade under sustained high heat. While standard central heating systems operate safely at 82°C, SharkBite fittings’ 93°C continuous rating makes them unsuitable for high-heat industrial applications.
Environmental challenges present additional risks. Ice expansion during freezing exceeds pressure thresholds, causing catastrophic failures in unheated spaces like caravans and boats. I’ve seen vibration in mobile installations loosen joints despite proper mounting. UV exposure degrades plastic components over time, while thermal cycling accelerates material fatigue. Chemical compatibility remains limited – these fittings resist mild acidic conditions but fail when exposed to aggressive solvents or extreme pH levels. When used underground, brass push fittings require silicone tape wrapping for proper certification and protection against soil conditions.
Structural Support Challenges and Pipe Movement Issues
Beyond environmental constraints, push-fit connectors face critical challenges from inadequate structural support and pipe movement that can compromise joint integrity over time. I’ve observed that improper installation creates the most significant vulnerabilities—when you don’t fully insert pipes to their insertion marks, the collet teeth can’t achieve proper grip strength.
Repeated drain-and-refill cycles cause incremental pipe movement within fittings, gradually weakening connections. Without adequate pipe supports at regular intervals, sagging creates pull-out forces that exceed the collet’s retention capacity. High-vibration areas compound these issues, as constant movement loosens the mechanical grip.
I always recommend checking insertion marks visually, installing supports every 500mm, and avoiding push-fit placement near vibrating equipment. Regular inspections help identify movement before failure occurs. When expansion vessels fail, the resulting pressure fluctuations can create vacuum formation in pipe sections that introduces air and further destabilizes push-fit connections.
Insurance and Warranty Complications With DIY Installation
While structural vulnerabilities create immediate performance risks, push-fit connectors present equally serious long-term financial hazards through insurance coverage restrictions and warranty complications.
I’ve discovered that many insurers exclude push-fit systems entirely or impose higher excess fees specifically for DIY installations. Your property could face coverage denial for water damage claims, particularly during renovations. With escape-of-water incidents costing insurers over £1,000,000 per major claim, they’re increasingly restrictive.
DIY errors void manufacturer warranties immediately—incomplete pipe insertion or inadequate support leaves you completely liable. I’ve seen domestic claims average £200,000 for self-builders, with filing claims spiking future premiums by 20-50%. Poor workmanship with push-fit installations consistently ranks as the leading cause of escape-of-water claims across the UK.
You’ll protect yourself by consulting insurers pre-installation, pressure-testing systems, and maintaining professional documentation.
Conclusion
I’ve outlined the critical disadvantages that’ll impact your plumbing projects and bottom line. From installation errors causing water damage to material compatibility issues and insurance complications, push-fit connectors demand careful consideration. You’ll need proper training, quality tools, and adherence to manufacturer specifications to avoid costly failures. Don’t compromise on professional standards—the convenience isn’t worth the risk of catastrophic leaks, insurance claims, or structural damage that’ll far exceed initial savings.
References
- https://www.self-build.co.uk/push-fit-plumbing-what-can-go-wrong/
- https://www.professionalbuildingsupplies.co.uk/plumbing/is-push-fit-plumbing-reliable
- https://www.youtube.com/watch?v=NfFvliKdQ2Q
- https://community.screwfix.com/threads/pushfit-fittings.61333/
- https://forum.buildhub.org.uk/topic/3894-plumbing-push-fit-or-copper/
- https://www.cuspuk.com/wp-content/uploads/2023/03/Escape-of-water-in-buildings-due-to-plastic-pipe-plumbing-failures.pdf
- https://www.hawkins.biz/insight/push-fit-fittings-and-statistical-analysis/
- https://asbp.org.uk/resource-report/escape-of-water-in-buildings-due-to-plastic-pipe-plumbing-failures
- https://www.pbctoday.co.uk/news/building-control-news/escape-of-water-claims/81378/
- https://www.imia.com/wp-content/uploads/2023/07/IMIA-WGP-54-Water-Damage-5th-final-070710AW.pdf