I’ve spent years maneuvering through the complexities of UK building regulations, and I can tell you that fire-resistant plasterboard compliance isn’t just about ticking boxes—it’s about protecting lives and property. When you’re planning your installation, you’ll need to understand that the minimum 30-minute fire resistance requirement is only the starting point. There are critical material specifications, installation techniques, and system performance standards that can make or break your project’s safety credentials and regulatory approval.
Key Takeaways
- UK Building Regulations require minimum 30-minute fire resistance for structural elements using 12.5mm fire-rated plasterboard.
- Integral garages must have 30-minute fire separation from living spaces to prevent fire spread.
- Metal framing with 400mm stud spacing and three-coat fire-rated joint treatment ensures proper installation.
- Non-compliance can result in unlimited fines, insurance invalidation, and costly remedial work requirements.
- Whole-system performance validation is mandatory, not just individual component ratings for regulatory compliance.
Understanding Fire Resistance Ratings and Classifications
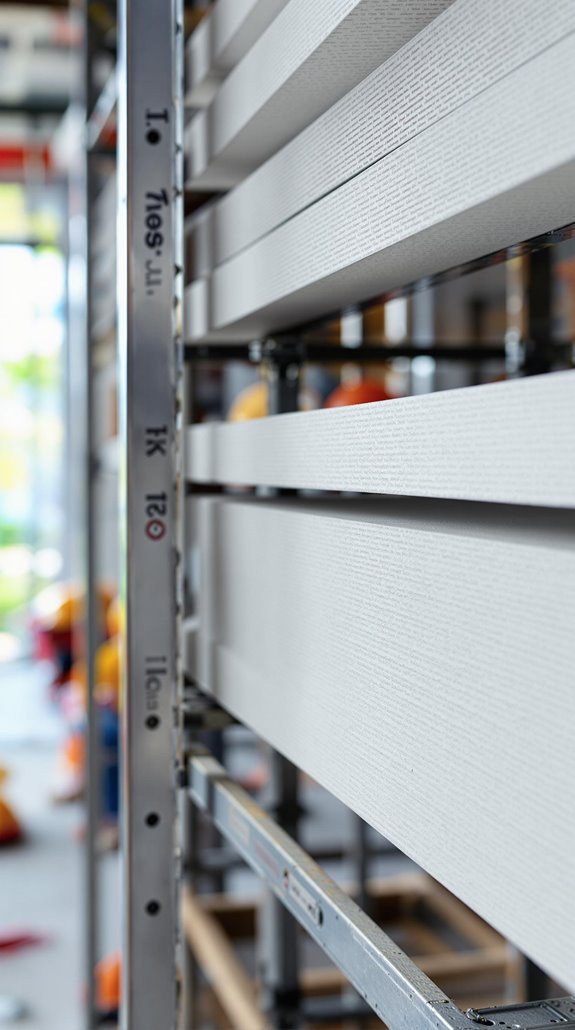
When specifying fire-resistant plasterboard systems, understanding the numerical ratings and classification frameworks becomes critical for proper material selection. I’ll break down the key systems you need to know.
Fire resistance ratings work on time-based measurements – typically 30, 60, 90, 120, or 180 minutes. These numbers indicate how long the board can withstand fire exposure. Single-layer systems using 12.5mm boards typically achieve 30 minutes, while 15mm boards reach 60 minutes.
The Euroclass system provides another classification layer. Standard fire-rated plasterboard achieves A2-s1,d0 classification, meaning limited combustibility with minimal smoke and droplet production. The fire resistance effectiveness stems from the calcination process, where heat dehydrates the gypsum core starting from the exposed surface and progressing inward. Specialized boards like Glasroc F can achieve A1 – the highest non-combustible rating. UK Building Regulations classify plasterboard as “material of limited combustibility,” giving surfaces Class 0 designation for low flame spread risk.
UK Building Regulations Compliance Requirements
Building Regulations Approved Document B sets the legal framework that governs fire-resistant plasterboard installations across England and Wales. I’ll guide you through the key compliance requirements that directly impact your project.
For structural elements, you must achieve minimum 30-minute fire resistance using either 12.5mm fire-rated plasterboard or two layers of 9.5mm standard plasterboard with plaster finish. This ensures that your construction adheres to fire safety standards and protects occupants in the event of a fire. Integral garages in two-storey homes require 30-minute separation minimum from living spaces above.
Your joist spacing can’t exceed 600mm centres with minimum 38mm width. You’ll need tongue-and-groove floorboarding or hardboard overlay to block smoke penetration. Fire stopping of limited combustibility is mandatory at compartment wall junctions. Internal ceiling finishes must use Class 1-rated materials to prevent fire spread throughout the building.
Essential Applications for Fire-Resistant Plasterboard
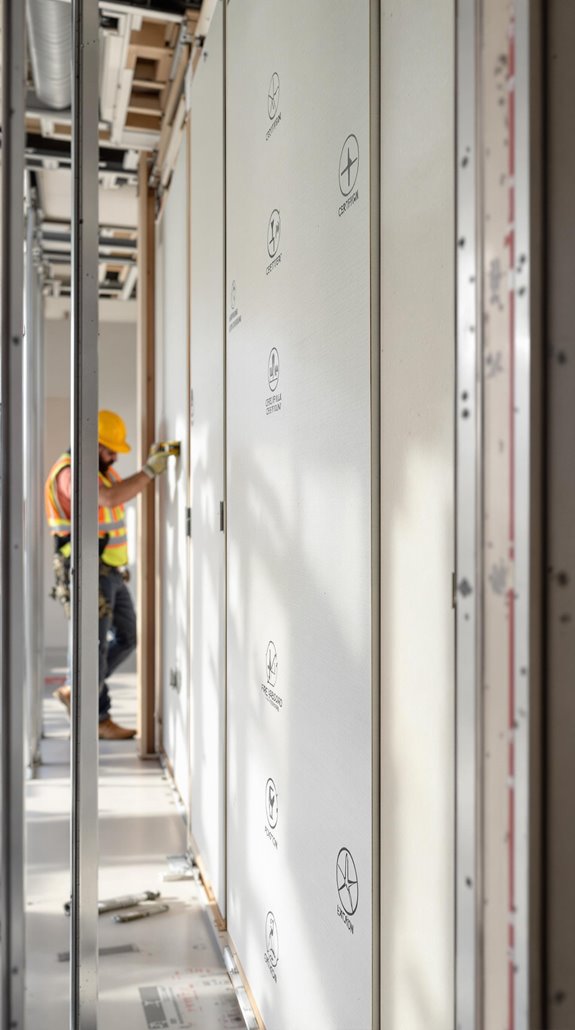
Fire-resistant plasterboard serves critical protective functions across diverse building applications where standard materials can’t meet safety requirements. I’ve seen it transform safety outcomes in garages, where it prevents fire spread from attached structures into living spaces through mandated fire-resistant barriers. In partition systems, it creates essential fire compartments that contain blazes within designated areas.
Historic renovations particularly benefit from fire-resistant plasterboard when traditional compliance methods aren’t feasible. I recommend it for asset protection applications like server rooms and archives, where replacing damaged contents costs more than prevention. Buildings housing vulnerable occupants—elderly residents, healthcare patients, or young children—require this enhanced protection most. The additional evacuation time it provides compensates for slower mobility, making it indispensable for meeting modern safety standards. Professional installation requires cutting with fine-toothed blades to prevent chipping and ensure proper fit.
Installation Best Practices and Professional Guidelines
Although standard plasterboard installation techniques provide adequate performance for most applications, fire-resistant systems demand precision and adherence to specialized protocols that can’t be compromised. I’ll guide you through the critical elements that separate professional fire-rated installations from standard practice.
First, I recommend metal framing over timber studs for superior fire resistance. You’ll need to reduce stud centers to 400mm spacing and use self-drilling drywall screws with corrosion protection at 200mm intervals. Don’t skip the three-coat joint treatment using fire-rated compounds and paper tape—mesh tape won’t deliver the same fire performance. Proper installation is essential for achieving fire-resistant properties that meet safety standards.
Around openings, install Gyproc CoreBoard packers with Gypframe Retaining Channels. Remember, 15mm boards outperform 12.5mm variants for extended protection periods. When installing multiple layers, ensure you stagger joints by a minimum of 300mm and provide complete systems approach rather than relying solely on board specifications.
Material Specifications and Performance Standards
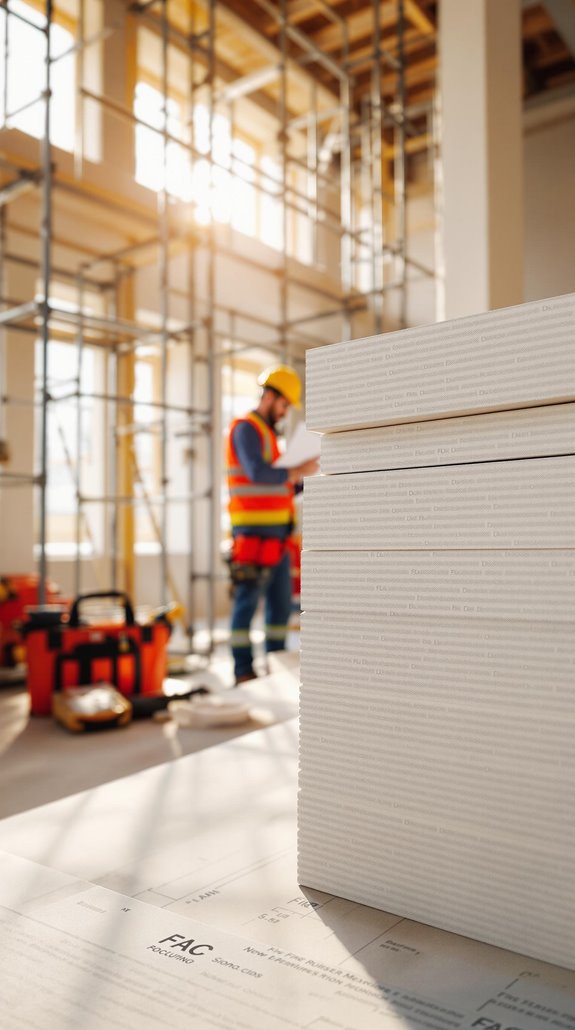
When specifying fire-resistant plasterboard, you’ll encounter distinct material compositions engineered to exceed standard performance thresholds through enhanced gypsum formulations and specialized additives. I recommend identifying boards by their pink color coding, which distinguishes fire-rated products from standard variants. You’ll find the crystallized water within the gypsum core releases vapor under heat, effectively slowing temperature rise during fire exposure.
The enhanced fiber reinforcement I specify maintains structural integrity throughout thermal stress. For specialist applications, I select boards containing non-combustible glass fibers or vermiculite additives, achieving superior density compared to standard plasterboard. The calcination process absorbs heat and stabilizes temperature at 100°C, forming a protective calcined layer that retains structural integrity. These materials must meet Euroclass A1 or A2-s1,d0 classifications, ensuring limited combustibility. When you’re selecting products, verify they comply with BS 476-7 Class 1 surface spread requirements for ideal fire performance.
Regulatory Updates and Timeline Changes
Understanding these material specifications becomes considerably more complex as regulatory frameworks undergo substantial changes across the coming years. I’ll guide you through the critical shift from BS 476 to European EN standards, starting March 2025 with full compliance required by September 2029.
You’ll need to adapt to the Euroclass system (BS EN 13501-1), which demands A2-s1-d0 ratings or higher for external walls in buildings over 11 meters. I’m particularly concerned about the increased 60-minute fire resistance requirements for cavity barriers in high-risk buildings.
Building control bodies are prioritizing these 2025 updates during inspections, and insurance firms won’t provide coverage without proof of compliance. The transition will emphasize whole-system performance rather than individual component testing, fundamentally changing how we approach fire safety validation. The £15 billion remediation cost estimates underscore why getting this right matters for our industry’s future.
Cost Implications of Non-Compliance
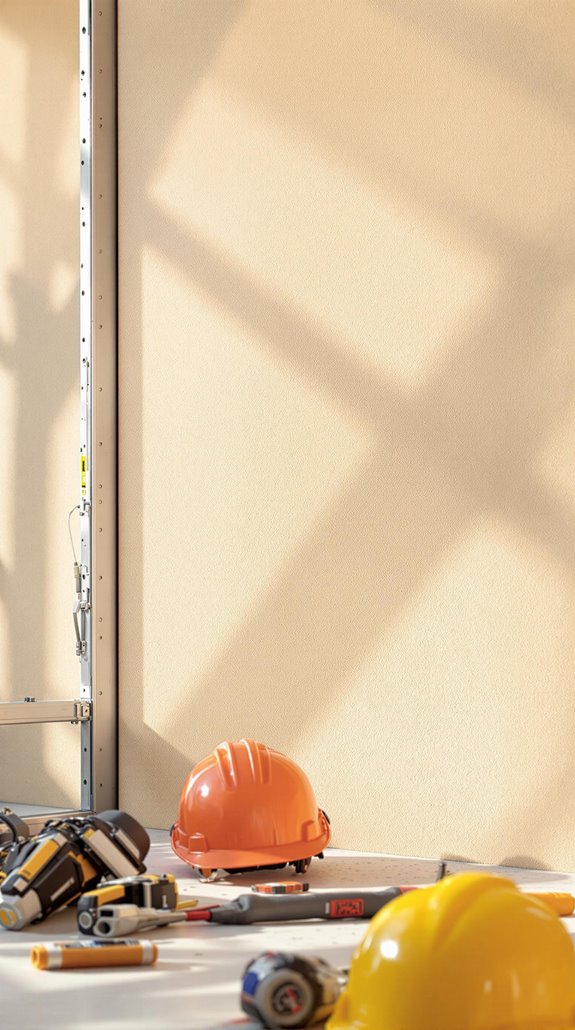
Since March 2025’s regulatory changes carry enforcement teeth, non-compliance with fire-resistant plasterboard requirements triggers cascading financial consequences that’ll devastate project budgets and property values.
I’ve seen remediation costs spiral when contractors must strip and replace standard plasterboard with compliant fire-rated alternatives. You’re looking at complete reconstruction costs, plus upgraded material expenses for 12.5mm or 15mm fire-rated boards that cost considerably more than standard options. Having professional inspections prior to project completion can help ensure compliance and avoid these costly issues.
Insurance implications hit harder—policies may be invalidated, claims rejected, and premiums increased. Local authorities can impose unlimited fines under building regulations, while enforcement notices demand immediate costly corrections. Fire-rated plasterboard’s distinctive pink paper face makes compliance violations immediately visible during inspections, leaving no room for ambiguity in enforcement actions.
Property devaluation becomes inevitable as mortgage lenders require compliance before lending, surveyors flag violations, and buyers negotiate price reductions to cover your compliance costs.
Whole-System Performance Vs Component Testing
Beyond the financial penalties that devastate non-compliant projects, there’s a fundamental misunderstanding that trips up most builders: thinking individual plasterboard ratings guarantee regulatory compliance.
I’ve seen countless projects fail because builders assume Class A1 plasterboard automatically meets Building Regs. Here’s the reality: component testing measures reaction to fire, not system performance. Your 12.5mm fire-resistant board might achieve excellent Euroclass ratings, but that’s meaningless without whole-system validation.
Fire ratings—30, 60, 90, 120 minutes—come exclusively from full-assembly tests. These evaluate complete systems under actual fire conditions, testing insulation, integrity, and load-bearing capacity simultaneously. For garage ceilings requiring rooms above, you’ll need dual-layer plasterboard with proper joints, finishing, and studwork integration. The calcination process begins at the fire-exposed surface and progresses through the gypsum layer, with the calcined material on exposed faces actually slowing down further calcination.
Documentation must prove tested system integration for regulatory compliance.
Conclusion
I’ve covered the critical aspects of fire-resistant plasterboard compliance, but you can’t afford to take shortcuts. You’ll need to verify current regulations, use properly rated materials, and guarantee professional installation. Don’t assume component testing equals whole-system performance—it doesn’t. Non-compliance isn’t just expensive; it’s potentially deadly. I’d strongly recommend consulting a qualified fire safety engineer before proceeding. Your building’s fire resistance depends on getting every detail right the first time.
References
- https://clairedouglasstyling.co.uk/post/is-plasterboard-fireproof-what-you-need-to-know
- https://www.buildershoponline.co.uk/news/Need-Fire-Resistant-Plasterboards-Here’s-some-helpful-hints
- https://gointeriors.co.uk/fire-resistant-plasterboard
- https://www.mdpi.com/2071-1050/1/3/674
- https://www.wall-systems.co.uk/fire-safety-regulations-are-changing/
- https://insulationgo.co.uk/plasterboards-wallboard-2400-1200-mm/fire-panel-a1-a2-knauf-12.5mm-15mm-2400mx1200mm-pink-promat-monolux-500-(mst-500)-non-combustible-board-fire-protection-240-minutes-6mm-glasroc-f-10mm-12.5mm-online-london-uk/
- https://diybuildingsupplies.co.uk/blogs/news/what-fire-rating-does-fire-resistant-plasterboard-provide
- https://ewipro.com/2023/11/04/fire-resistance-in-uk-building-regulations/
- https://www.british-gypsum.com/products/board-products/gyproc-fireline-12-5mm
- https://buildingcontrol.bathnes.gov.uk/loft-conversions/fire-safety