I’ve been investigating spray foam insulation issues across the UK, and what I’ve discovered will fundamentally change how you view this seemingly beneficial home improvement. Major lenders like TSB and Aviva aren’t just being cautious—they’re protecting themselves from a mounting crisis that’s already destroyed property values and left homeowners facing five-figure remediation costs. The technical failures I’ve documented reveal systemic problems that most installers won’t discuss, and the consequences extend far beyond simple moisture damage.
Key Takeaways
- 25% of major UK lenders reject mortgage applications for properties with spray foam insulation due to structural damage risks.
- Spray foam can trap moisture causing timber decay, mold growth, and remediation costs reaching £25,000-£30,000.
- Open-cell foam is unsuitable for British climates as it absorbs moisture and permits dangerous water vapor transmission.
- Professional removal costs £2,000-£5,000 for 3-bedroom properties, with insurance not covering mortgage-related removal expenses.
- Homeowners can pursue compensation through small claims court or specialist solicitors for installer negligence and structural damage.
Why Major UK Lenders Are Refusing Mortgages for Spray Foam Properties
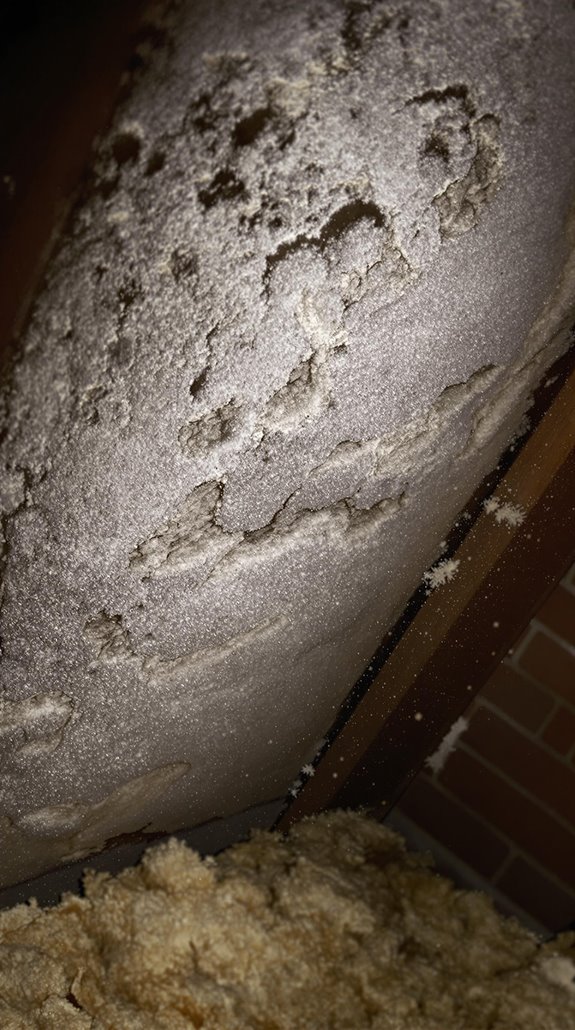
When spray foam insulation was first marketed as an energy-efficient solution, most homeowners didn’t anticipate it would create a mortgage crisis. Today, 25% of major UK lenders—including TSB, Skipton, and Aviva—reject mortgage applications outright for properties with spray foam insulation.
I’ve seen how lenders categorize these properties as unacceptable liability exposures due to hidden structural damage risks. When foam traps moisture against roof timbers, it causes wood rot that surveyors can’t detect until severe damage occurs. This creates remediation costs reaching £25,000–£30,000.
Even lenders offering case-by-case approvals require £1,500+ structural surveys with uncertain outcomes. Properties face valuation reductions or “unmortgageable” classifications, making buyers avoid them entirely due to future resale difficulties. The problem extends beyond mortgages, as insurance companies may also refuse coverage for properties with spray foam insulation.
The Hidden Condensation Crisis Destroying British Homes
Behind these mortgage rejections lies a fundamental engineering problem that’s silently destroying British homes: spray foam insulation creates condensation crises that compromise structural integrity. When you install spray foam incorrectly, it disrupts the natural ventilation that’s absolutely essential for managing moisture in our damp climate.
Here’s what’s happening in thousands of homes: warm, moist air from your living spaces meets cold roof surfaces, creating perfect conditions for condensation. Without adequate ventilation pathways, this moisture becomes trapped, leading to timber decay, mold growth, and structural damage that can cost tens of thousands to repair. Proper insulation methods can help mitigate these issues by ensuring that homes maintain their thermal efficiency without compromising air quality.
The problem isn’t just cosmetic—it’s destroying the very bones of British housing stock, which is why lenders are running scared. The critical issue becomes even more complex when dealing with open-cell foam, which cannot act as a vapor barrier and allows moisture penetration directly into structural elements.
Open-Cell Vs Closed-Cell: Understanding the Critical Material Differences
Open-cell foam’s interconnected air pockets create a sponge-like texture that absorbs moisture, making it unsuitable for humid British climates. It offers R-3.5 to R-4 per inch but permits dangerous water vapor transmission. Additionally, implementing internal wall insulation can serve as a complementary solution to help manage moisture levels in homes.
Closed-cell foam features sealed gas pockets forming a rigid, waterproof barrier. With R-6 to R-7 per inch—nearly double open-cell’s capacity—it blocks moisture ingress while providing structural integrity. The HFO blowing agents used in closed-cell formulations contribute to global warming concerns, though newer formulations are improving environmental performance.
I’ve seen countless homeowners choose open-cell for cost savings, only to face expensive remediation when condensation destroys their investment. For UK conditions, closed-cell’s vapor barrier properties aren’t optional—they’re essential for preventing the moisture disasters plaguing British homes.
The Shocking Truth About Spray Foam Removal Costs and Complications
If you’re facing spray foam removal, prepare for costs that’ll shock you into reconsidering your original installation decision. I’ve witnessed homeowners face £2,000-£5,000 bills for professional removal from 3-bedroom properties, averaging £40 per m². That’s 10x standard insulation removal costs.
You can’t tackle this yourself without risking permanent timber damage and toxic dust exposure. The process requires specialised heated scrapers, industrial vacuums, and licensed hazardous-waste disposal. Closed-cell foam’s rigidity makes removal even costlier than open-cell variants.
Your insurance won’t cover removal linked to mortgage refusals. Add structural repairs (20-50% cost increase), reinsulation (£1,500-£3,000), and disposal fees (£100-£300). London properties face 25% premiums above national averages. Smart homeowners are booking removal during off-peak seasons to reduce these already devastating costs. We’re part of a community learning expensive lessons about spray foam’s hidden consequences.
How Government Schemes Accidentally Created a Housing Crisis
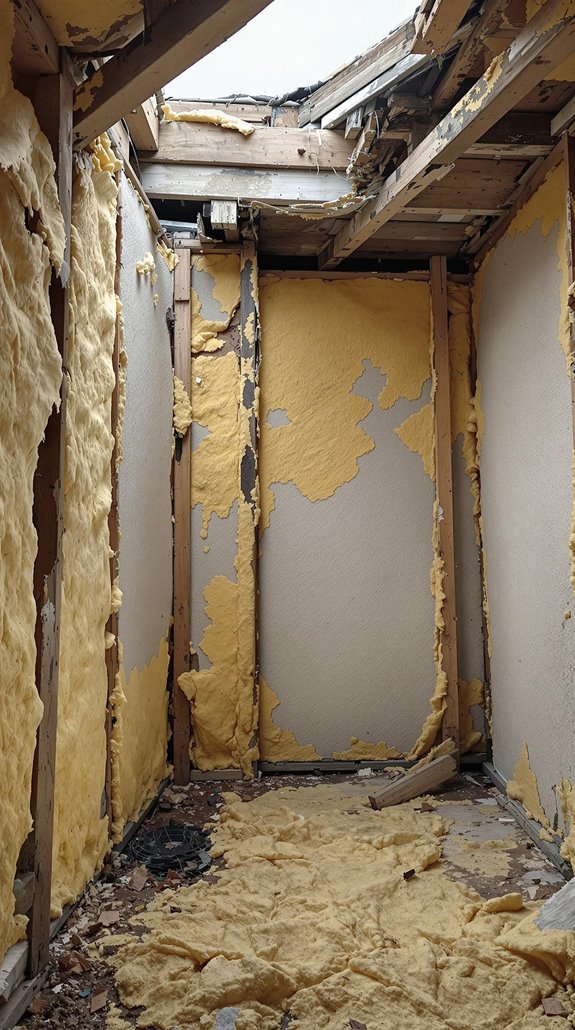
The government’s well-intentioned energy efficiency schemes have released an unprecedented wave of problematic installations across Britain’s housing stock. I’ve witnessed how the rapid scaling of programmes like ECO and GBIS has created perfect conditions for spray foam disasters.
The numbers tell the story: 420,600 installations in 2024 alone, with ECO growing 24% year-on-year. This breakneck pace has overwhelmed quality controls, particularly affecting the 90% of solid-wall properties that lack proper insulation. What’s most concerning is the absence of mandatory quality verification for spray foam installations. Additionally, the lack of typical renovation projects has made it challenging for homeowners to understand the implications of their choices.
The £1 billion GBIS funding has incentivized volume over precision, targeting council tax bands A-E without technical suitability assessments. By March 2025, the scheme had already installed 76,900 measures across 60,600 households, demonstrating the massive scale of potential risk exposure. We’re seeing retrofit complexity systematically underestimated, with no post-installation monitoring to catch failures before they become catastrophic.
Essential Steps for Homeowners Already Affected by Spray Foam Issues
When spray foam problems strike your property, swift action becomes vital to prevent escalating damage and financial losses. I’ll guide you through the essential steps that protect your investment and restore your home’s integrity.
First, arrange a professional inspection immediately. You’ll need certified experts who can identify installation defects, conduct moisture testing, and assess structural damage. Don’t risk DIY approaches—hire qualified professionals for mechanical removal, budgeting minimum £3,000 for the process. Early detection of subsidence issues is crucial to avoid more extensive repairs later.
Document everything meticulously. Obtain removal certificates, photographic evidence, and structural surveys. These records are important for mortgage applications and future transactions. Remember that mortgage applications can be denied when spray foam issues are discovered, making thorough documentation even more critical. Post-removal, replace compromised timbers and enhance ventilation systems.
Finally, explore your legal options. If you’re part of government schemes, investigate potential mis-selling claims and report non-compliant installers to Trading Standards.
Warning Signs That Your Spray Foam Installation Has Failed
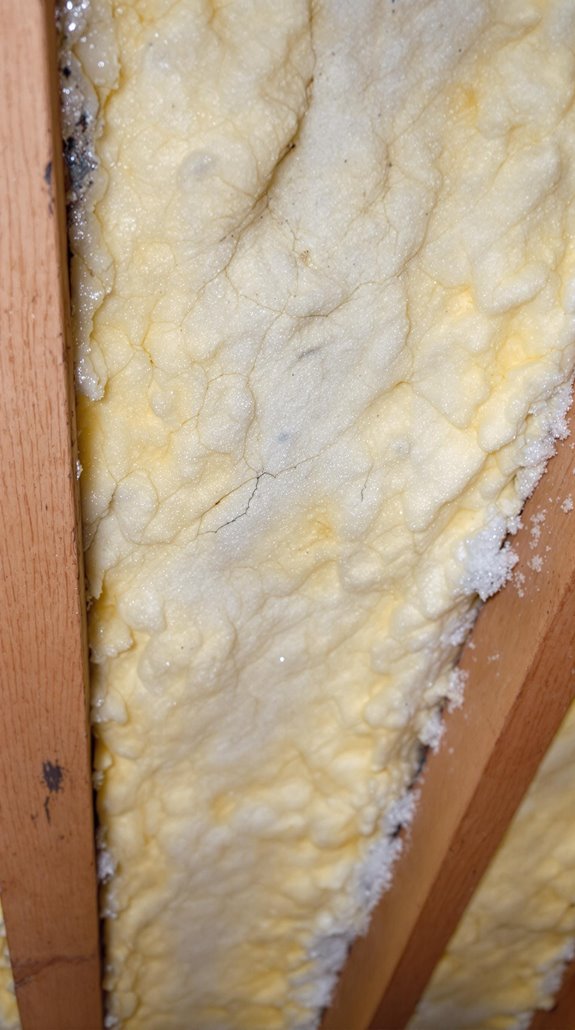
Although spray foam insulation failures can develop gradually over months or years, recognising the early warning signs enables you to address problems before they escalate into costly structural damage.
I’ve identified five critical indicators that signal spray foam failure. First, persistent musty odours and visible mould growth indicate moisture accumulation behind the foam barrier. Second, structural issues manifest through roof tile displacement, visible gaps between rafters and foam, and cracking sounds during temperature changes. Third, thermal performance deficiencies appear as ice dam formation, inconsistent room temperatures, and unexpectedly high energy bills. The impermeable nature of closed-cell spray foam prevents airflow passage, creating conditions where condensation becomes trapped against timber surfaces. Fourth, health symptoms including respiratory irritation, headaches, and aggravated asthma suggest off-gassing issues. Finally, missing certification documents, warranty paperwork, and condensation risk assessments indicate substandard installation practices that increase failure likelihood.
Legal Rights and Recourse Options for Damaged Property Owners
Property owners facing spray foam insulation failures aren’t powerless against the financial and structural damage these installations can cause. You have several legal avenues to pursue compensation and remediation. It is crucial to understand your rights under party wall agreements when dealing with adjacent properties impacted by insulation issues.
I’ll walk you through your strongest options. Small claims court handles damages under £10,000 without requiring legal representation, making it accessible for most property damage cases. For larger claims, specialist solicitors can pursue negligence lawsuits against installers who violated safety standards or caused structural deterioration.
Document everything: contracts, sales brochures, emails, and independent structural surveys confirming damage causation. If you’ve experienced mortgage refusal or property devaluation, file complaints with the Financial Ombudsman for finance-related mis-selling.
Consider group litigation if multiple homeowners in your area face similar issues—collective action strengthens your position against companies using deceptive practices. Registration is typically required to join group actions targeting installers or companies involved in widespread mis-selling under government schemes.
Alternative Insulation Solutions That Won’t Destroy Your Home’s Value
After experiencing spray foam disasters, homeowners need proven alternatives that deliver superior thermal performance without compromising their property’s structural integrity or market value.
I’ve researched the most effective alternatives that mortgage lenders actually approve. Knauf Insulation, composed of recycled glass and natural sand, offers outstanding thermal performance with effective acoustic properties. It’s environmentally friendly and installs easily in lofts, walls, and floors without harmful chemicals, aligning with sustainable building practices.
Actis Hybris represents the industry-leading spray foam alternative, preventing moisture-trapping and timber decay while maintaining mortgage approval prospects. Fibreglass insulation remains one of the most affordable options, available in blanket or loose-fill forms using recycled glass materials.
These alternatives prevent mould growth, avoid mortgage refusal, eliminate expensive removal procedures, and maintain property value through sustainable, eco-friendly materials that protect your investment. Unlike spray foam, these solutions allow for proper visual inspection of structural elements, preventing hidden termite infestations and undiscovered damage.
Conclusion
I’ve outlined the critical spray foam insulation challenges you’re facing as a UK homeowner. You now understand why lenders reject these properties, recognize the moisture risks, and know the material differences between foam types. I’ve provided practical steps for affected homeowners and alternative solutions that won’t compromise your property’s value. Don’t let spray foam destroy your investment—take action now to protect your home’s structural integrity and marketability.
References
- https://buildreview.org/spray-foam-insulation-troubles/
- https://propertyinspect.com/uk/blog/spray-foam-insulation-guide-2024/
- https://hoa.org.uk/advice/guides-for-homeowners/i-am-improving/spray-foam-roof-insulation/
- https://commonslibrary.parliament.uk/spray-foam-insulation-and-mortgages/
- https://www.youtube.com/watch?v=hCZgv4K5aTk
- https://todaysconveyancer.co.uk/major-lenders-refuse-to-lend-on-property-with-spray-foam-insulation/
- https://swiftsprayfoamremoval.co.uk/5-reasons-mortgage-lenders-refuse-properties-with-spray-foam/
- https://www.leadingpropertylawyers.co.uk/mortgage-lenders-refuse-loans-on-properties-with-spray-foam-insulation/
- https://countrywideinsulation.co.uk/blog/spray-foam-removal-blogs/why-mortgage-lenders-are-asking-for-spray-foam-removal-certificates
- https://insulation-more.co.uk/blogs/the-pipe-duct-lagging-expert/will-spray-foam-insulation-stop-condensation