I’ve spent years watching concrete block walls fail prematurely, and the culprit is almost always the mortar mix. You can’t simply grab any cement and sand combination from your local supplier and expect lasting results. The UK’s demanding climate requires specific ratios, proper mortar designations, and compliance with BS EN 998-2 standards. Get this foundation element wrong, and you’ll face costly repairs within a few seasons. Here’s what separates amateur blockwork from professional-grade construction.
Key Takeaways
- Use Type N mortar (1:1:6 cement:lime:sand ratio) for general concrete blockwork applications in the UK.
- Apply M6 class mortar with 1:½:4.5 ratios for load-bearing walls and external applications requiring structural integrity.
- Follow 4:1 sand-to-cement ratio for standard projects, or 3:1 for high-stress structures like retaining walls.
- Ensure compliance with BS EN 998-2:2016 standards, declaring compressive strength classes from M1 to M20.
- Add lime to improve workability and flexibility, helping mortar accommodate slight movements without cracking.
Understanding Mortar Mix Ratios for Concrete Block Construction
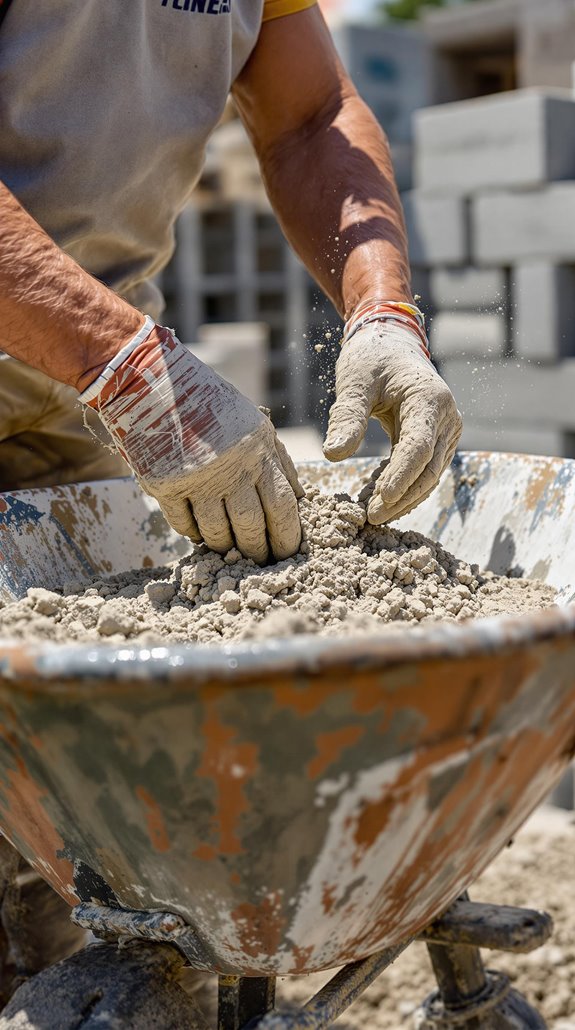
Three fundamental mortar types dominate concrete block construction, each defined by specific cement-to-lime-to-sand ratios that determine performance characteristics.
I’ll break down the essential ratios you need to know. Type S mortar uses 1 part cement, 1/2 part lime, and 4-1/2 parts sand, delivering high strength for below-grade applications. Type N mortar combines 1 part cement, 1 part lime, and 6 parts sand, providing moderate strength for general blockwork. For straightforward projects, I recommend the simple 4:1 sand-to-cement ratio without lime.
The lime addition isn’t just filler—it dramatically improves workability and flexibility. When you’re laying blocks, lime creates a more forgiving mortar that accommodates slight movement without cracking. Understanding these ratios guarantees your blocks bond properly and withstand UK weather conditions effectively. Proper material quality ensures consistent performance, as variations in cement, sand, and water purity directly affect your mortar’s final strength and durability.
Standard Mix Proportions: Cement, Lime, and Sand Combinations
When selecting mortar proportions for concrete blocks, understanding the precise cement-lime-sand combinations guarantees structural integrity and workability. I’ll guide you through the standard UK mix that’s proven reliable for countless builders.
For concrete blockwork, I recommend the 4:1 sand-to-cement ratio as your foundation. This translates to 4 parts sand and 1 part cement for standard applications. When you’re tackling retaining walls or high-stress structures, I’d shift to a stronger 3:1 ratio—3 parts sand to 1 part cement.
Adding lime transforms your mix’s performance. For medium-strength applications, I use 1 part cement, 1 part lime, and 6 parts sand. This combination delivers excellent workability while maintaining adequate strength for above-grade walls you’ll depend on. Remember that excess water in your mortar mix can lead to poor adhesion of blocks, compromising the overall bond strength.
Mortar Designations and Strength Requirements for UK Building Standards
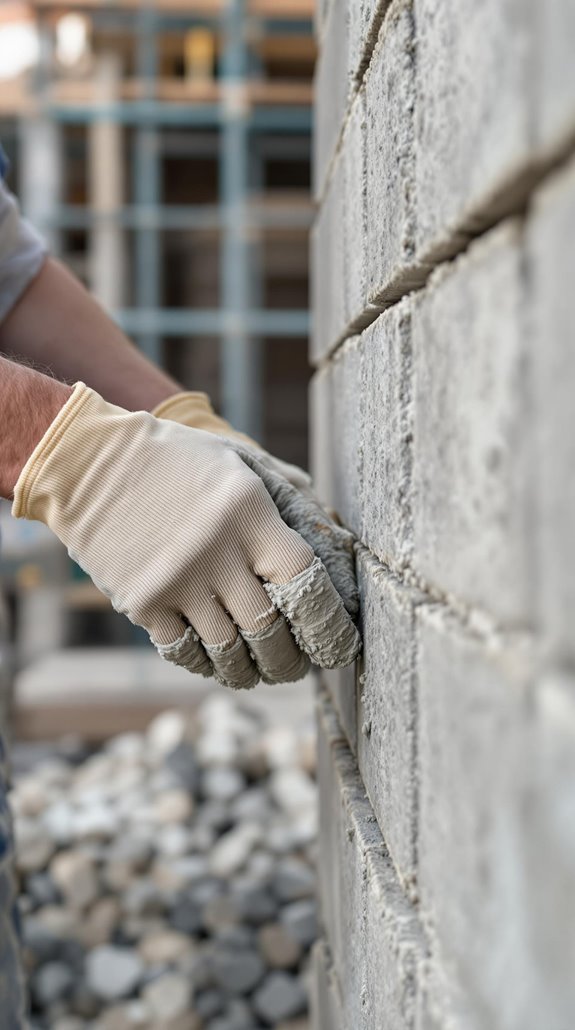
Understanding these fundamental mix proportions prepares you for steering through UK building standards, where mortar designations carry specific strength requirements that determine structural performance. I’ll guide you through the classification system that governs our practice.
Class M12 mortar delivers 12 N/mm² compressive strength for reinforced blockwork and high-stress applications. You’ll use Class M6 (6 N/mm²) as your standard for below-ground blockwork facing saturation and freezing risks. Lower-strength mortars like Type O serve non-load-bearing walls exclusively.
BS EN 1996-2:2006 and PD 6697 define these requirements, while BS 5628 Part 1 specifies characteristic flexural strength by unit type. Remember: your mortar strength must exceed structural demands without over-strengthening, which prevents unit damage and maintains proper load distribution.
Selecting the Right Mix for Different Concrete Block Applications
Since concrete blocks vary dramatically in density, load requirements, and exposure conditions, I’ll match your mortar selection to specific application demands rather than rely on generic solutions.
For standard internal partitions, you’ll want M2 designation with 1:2:8-9 ratios—this maximizes cost efficiency while providing adequate bonding strength. Load-bearing walls demand M6 mixes at 1:½:4-4.5 ratios, ensuring structural integrity under heavy loads without compromising workability.
External walls in severe UK weather require M6 designation with air entrainers for freeze-thaw resistance. The reduced sand content (≤4.5 parts) minimizes water penetration risks that cause spalling. Measuring the void ratio of your sand is essential since different sand types can significantly affect binder requirements and overall mortar performance.
Historic restoration projects need softer M2/M4 mortars using traditional lime-rich formulations. These prevent thermal movement damage while maintaining material compatibility with aged masonry systems.
Essential Mixing Techniques for Consistent Results
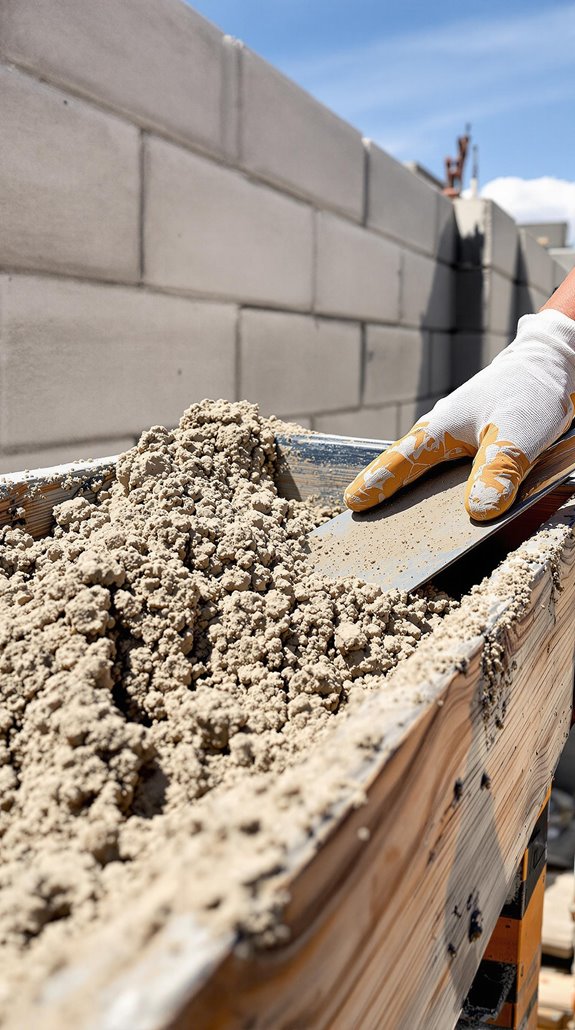
Although mortar appears straightforward to mix, achieving consistent results requires precise technique and systematic approach. I’ll share the essential methods that guarantee your concrete block mortar performs reliably every time.
Start with dry mixing – measure your sand, cement, and lime accurately, then combine them on a clean surface. Create a crater in the center for even distribution, mixing until you achieve uniform color and texture without lumps.
Add water gradually, using only half your estimated amount initially. I recommend incorporating any plasticizers into the water first for even distribution. Mix thoroughly after each addition until you reach a stiff, workable consistency that holds its shape.
Test your mix by creating a ridge with your trowel – it should stand without excessive collapse, allowing easy spreading without sliding off. Work in small batches to maintain quality, as mixed mortar should be used within 2 hours to prevent hardening.
Volumetric Batching: Achieving Accurate Measurements Every Time
When precision matters most in concrete block construction, volumetric batching delivers unmatched accuracy by measuring raw materials through volume rather than weight. I’ve found this system transforms how we approach mortar mixing through separate onboard compartments for cement, aggregates, water, and additives.
The equipment’s flow meters and calibrated augers regulate material discharge while sensors monitor real-time flow to prevent deviations. You’ll appreciate the high-energy auger that combines materials in 5-10 seconds, ensuring complete hydration and uniform encapsulation.
What sets volumetric batching apart is its waste reduction—I’ve seen 15-20% less leftover material compared to drum mixers. The system produces exact project volumes, enables small-batch production without efficiency loss, and provides volume-based billing transparency that matches usage to cost. With approximately 1,000 VCMs currently operating across the UK, this technology has established itself as a significant component of the concrete delivery sector.
Additives and Enhancements for Superior Performance
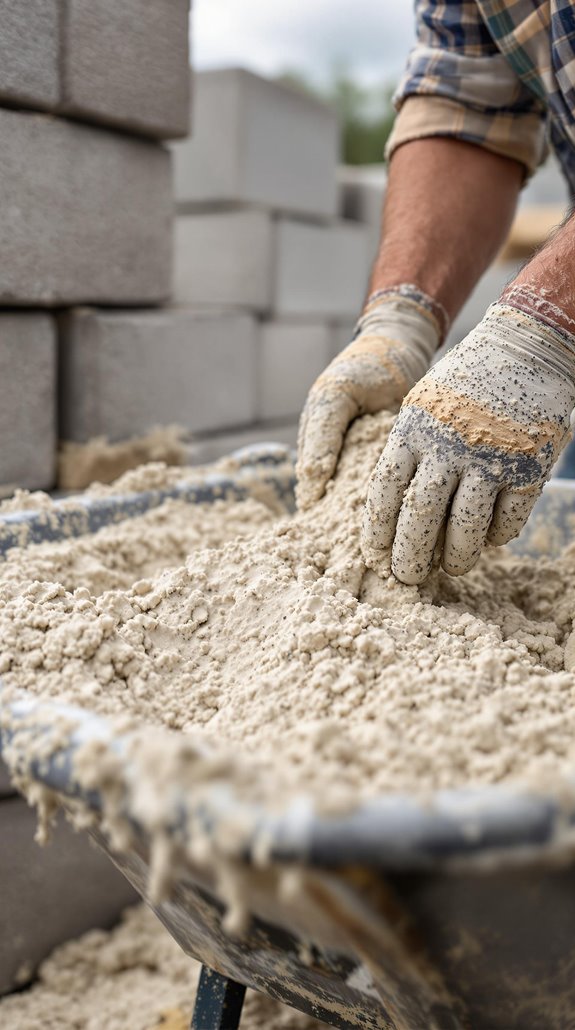
While volumetric batching guarantees precise material ratios, additives and enhancements transform ordinary mortar into high-performance systems that exceed standard construction requirements.
I’ll focus on proven admixtures that deliver measurable benefits for concrete block construction. Water-reducing plasticizers let you achieve superior workability while maintaining strength, even with weaker 1:5 cement-sand ratios. Air-entraining plasticizers introduce microscopic bubbles that boost freeze-thaw resistance—essential for UK conditions.
You’ll see 25-40% improved durability against water ingress when following BS EN 934-3 dosing protocols. Lime additives enhance workability and reduce shrinkage cracking by up to 30%. However, overdosing plasticizers increases porosity by 15-20%, compromising water resistance.
Stick to manufacturer instructions and avoid combining masonry cement with additional admixtures—you risk accidental overdosing that weakens your mortar system. All admixtures must demonstrate established suitability before use to ensure compatibility with your specific mortar formulation.
BS EN 998-2 and BS 5628 Compliance Requirements
High-performance mortar means nothing without proper compliance documentation. I’ll guide you through the essential standards that govern our UK masonry work.
BS EN 998-2:2016 sets European requirements for masonry mortar, replacing the older 2010 version. You must declare compressive strength classes from M1 to M20, tested at 28 days using BS EN 1015-11 protocols. These differ from traditional UK designations you might know.
The National Annex NA bridges European standards with UK practices, ensuring compatibility with our existing BS 5628 code. Fresh mortar properties require declaration of workability, density, and air content. Chloride content can’t exceed 0.1% of dry mortar mass—critical for preventing reinforcement corrosion.
Eurocode 6 references EN 998-2 for mortar specification, making compliance essential for structural masonry applications.
Common Mixing Mistakes That Compromise Wall Strength
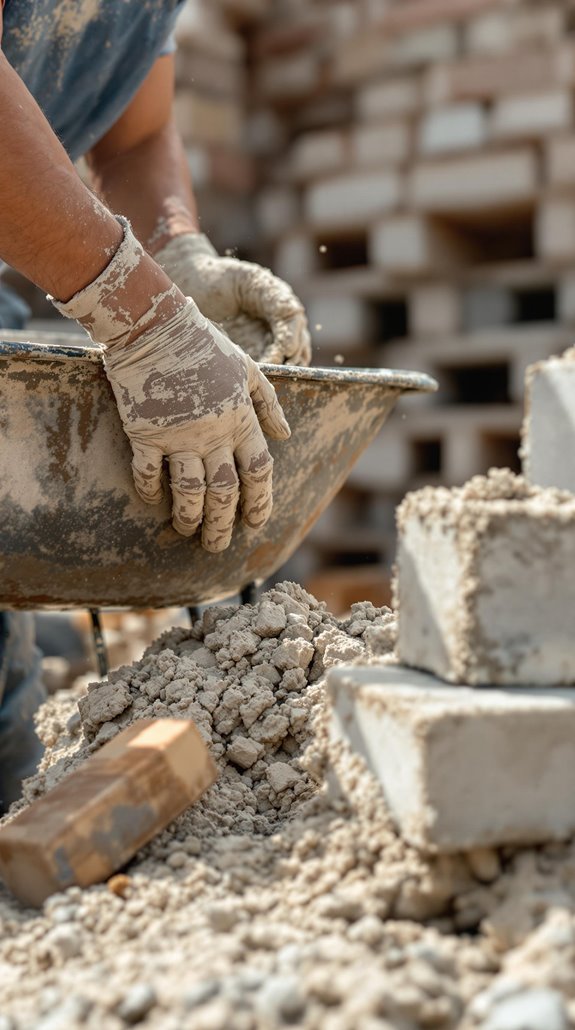
Despite understanding compliance requirements, many builders unknowingly sabotage their mortar’s structural integrity through fundamental mixing errors. I’ve witnessed countless failures from incorrect proportions—excess sand weakens cohesion while insufficient cement compromises adhesive strength. You’re risking block separation and reduced load-bearing capacity.
Inadequate mixing creates weak pockets through partial cement hydration. I can’t stress enough: thorough integration prevents clumped aggregates that concentrate stress points. Manual inconsistencies create batch variability, undermining your wall’s structural uniformity. Following manufacturer’s guidelines for water-to-cement ratios ensures optimal mixing consistency that directly impacts your final wall quality.
Weather conditions destroy your work faster than you’d expect. High temperatures induce shrinkage cracks, while frost exposure weakens crystalline bonds before setting. I’ve seen rainwater wash out cement particles, diluting critical compounds.
Using inappropriate sand types—exclusively fine building sand or unwashed contaminated varieties—introduces organic contaminants that hinder proper cement bonding, encouraging structural failure.
Professional Tips for Large-Scale Concrete Block Projects
Large-scale concrete block projects demand systematic planning and execution that goes far beyond mixing perfect mortar. I’ll share the professional strategies that separate successful builds from costly failures.
First, I establish laser-guided reference lines at corners before laying any blocks. This prevents cumulative errors across long spans. I verify plumb every third course—catching alignment issues early saves hours of remedial work.
For structural integrity, I embed vertical rebar at 1.2m intervals with 50mm concrete cover. In seismic zones, I install horizontal ladder reinforcement every fourth course. This creates monolithic strength that standard laying can’t achieve.
I cut blocks with diamond saws rather than altering structural bonds. Control joints every 6m manage thermal expansion, preventing random cracking. The thermal properties of concrete blocks help regulate temperature fluctuations that could compromise structural integrity over time. Finally, I laser-scan finished walls, maintaining ≤3mm tolerance variance across 10m spans.
Conclusion
I’ve covered the essential mortar mix ratios and techniques you’ll need for successful concrete block construction in the UK. Remember, a proper 4:1 sand-to-cement ratio works for most applications, while high-stress areas require 3:1 ratios. Don’t overlook BS EN 998-2 compliance requirements, and always maintain consistent mixing techniques. By following these guidelines and avoiding common mistakes, you’ll create durable walls that’ll withstand Britain’s challenging weather conditions and meet professional building standards.
References
- https://www.beesleyandfildes.co.uk/mortar-mix-ratios-and-cement-mixing/
- https://media.marshalls.co.uk/image/upload/v1611238100/Mortars-For-Concrete-Masonry-Products-BTB4.pdf
- https://lignacite.co.uk/wp-content/uploads/2023/01/Design-Guidance-Mortar.pdf
- https://www.buildingconservation.com/articles/mortar-mix-ratios/mortar-mix-ratios.html
- https://media.marshalls.co.uk/image/upload/v1729801087/Mason_Mix_Data_Sheet.pdf
- https://www.buildingmaterials.co.uk/info-hub/building-materials/mortar-mix-ratios
- https://www.diy.com/ideas–advice/building–hardware/cement-mortar–concrete/concrete-mix-ratios
- https://concreteflooringsolutions.co.uk/blog/understanding-concrete-mix-ratios-all-mixes-for-all-concrete-projects/
- https://www.homebuilding.co.uk/advice/mortar-mix
- https://www.ths-concepts.co.uk/how-to-calculate-wall-mortar-mix/